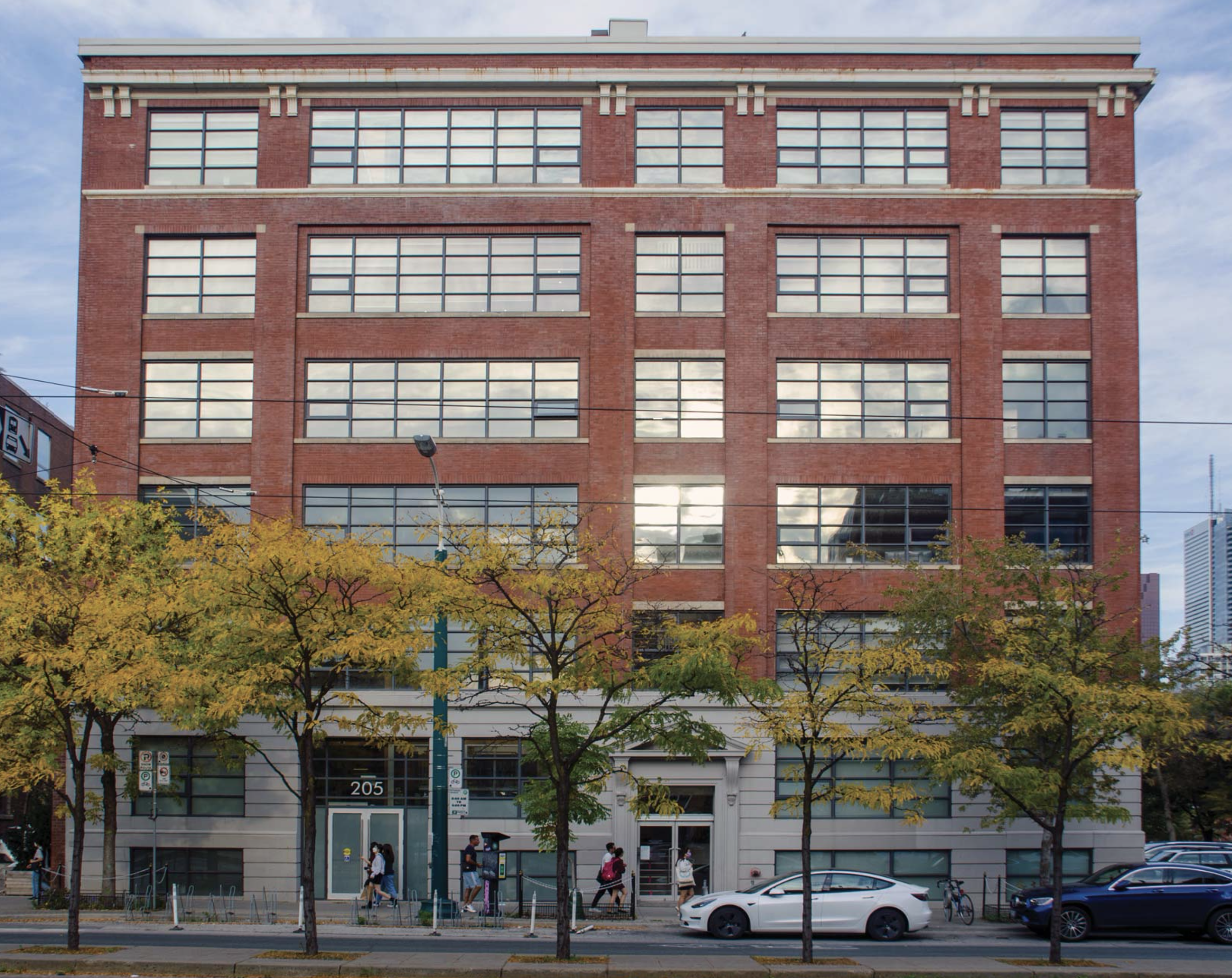
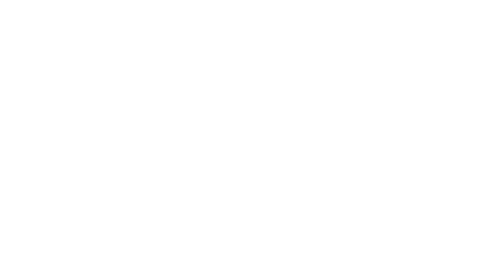
FEATURE
Lessons Learned:
Historical Tall-Wood Toronto
Scroll to Read
Humans have been building with wood since devising their earliest forms of primitive shelter. Unlike stone, wood proved a far more workable material that could be assembled by individual or small groups of workers. While it did not produce monumental architecture, it also did not demand decades of labour by a vast workforce. Quick and easy to construct, wood buildings proved to be durable and resilient while offering warmth and natural beauty. From the earliest European settlements to this day in Canada, wood accounts for most of our housing, and more recently we have witnessed the introduction of mass timber buildings that deploy a diverse palette of engineered wood products. It is predicted that a sustainable built environment will be founded on buildings that are constituted from an even higher proportion of bio-based materials than we use in conventional construction today, hence much of Canada's promise and destiny will continue to depend on her forests and the wood products they produce.
With our environment in mind, the advance of the contemporary "green" building movement continues to evolve, but a new vernacular of 21st century architecture with a sustainable ecological footprint has yet to fully emerge. While we seek to fashion reliable and robust recipes for our everyday buildings, ranging from apartments and stores, to schools and offices, there is much to learn from the resilient and adaptable warehouse and light-factory buildings that line the streets of Canada’s historic manufacturing districts.
A Typical Historical Tall-Wood Toronto Building
The Empire Clothing Factory, 197-205 Spadina Avenue, Toronto, Ontario was built in 1923, designed by Benjamin Brown, Architect. With over a century of commercial service in Toronto's garment district, this "brick and beam" building continues to house businesses and professional offices. The warm ambience of the interiors and ample daylighting and views on all four facades help maintain competitive rents in what remains a fully occupied income property. [Source: Historical Tall-Wood Toronto by Ross Beardsley Wood, 2024.]
Historical Tall-Wood Toronto is an evidentiary database of late 19th and early 20th century vernacular "brick and beam" buildings that were built using the fire restrictive specifications and methods of heavy timber mill construction in Toronto, Canada. But it is important to recognize this typology was also constructed across many parts of Canada and the United States, and everywhere it was built, it endured.
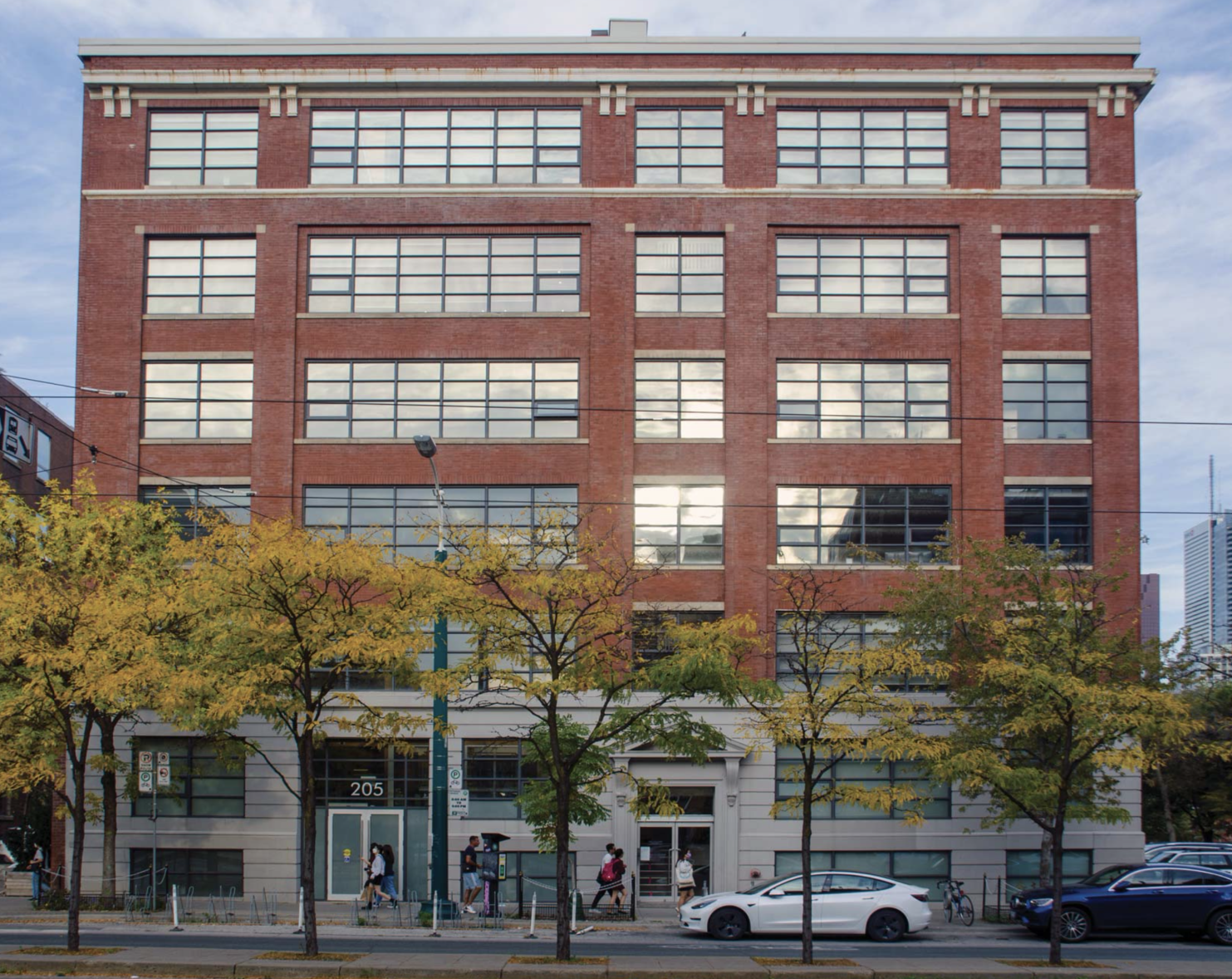
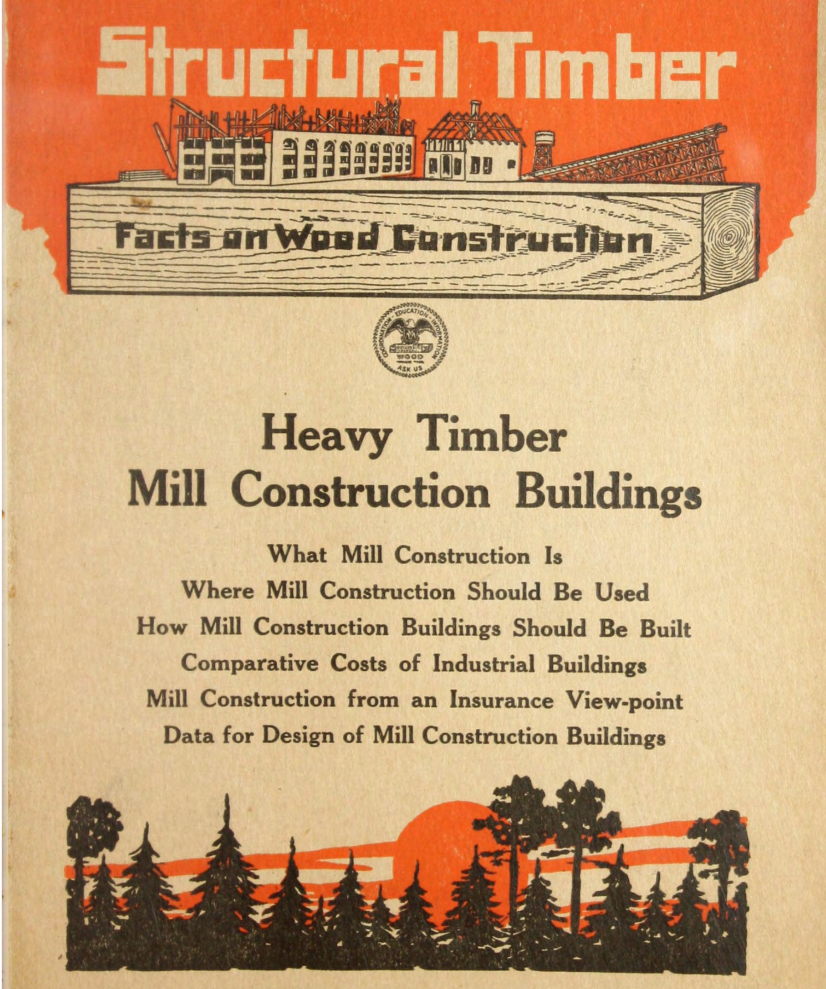
By the turn of the 20th century, heavy timber mill construction had become standardized and readily accessible technical guidance made available to architects, engineers and builders. This engineering bulletin from 1916 is an example of technology transfer by the lumber industry in America to promote mill construction for factories, warehouses and industrial buildings. Mill construction had evolved into a refined form of vernacular architecture that remains a distinctive and highly recognizable symbol of our industrialized society.
Heavy Timber Mill Construction
In the same way that light wood-frame house construction evolved into prescriptive codes and standards, mill construction pointed the way to the future of mass timber buildings whereby a series of formulaic design guidelines for common building archetypes would eliminate the need for alternative solutions to demonstrate code compliance. Complementary innovations in prefabricated modular building envelopes would enable rapid installation and subsequently, the periodic maintenance, retrofit and eventual replacement of enclosures over the building life cycle. Design for economy, efficiency, durability, flexibility/adaptability, resilience and low whole life carbon are key to the future of sustainable architecture. Our heritage "brick and beam" buildings did much of the heavy lifting needed to develop a contemporary sustainability framework for buildings crafted from wood.
This publication about Historical Tall Wood Toronto catalogues a cohort of such buildings that have endured and, in many ways, outperformed the vast majority of 20th and 21st century architecture. But this achievement can only be appreciated by taking the long view and considering the life cycle of buildings - the sort of design thinking that was baked into our historical tall-wood buildings, lessons learned that we must rediscover.
The term "mill construction" describes a type of building construction where interior framing and floors are of timber, arranged in heavy solid masses, and smooth flat surfaces, so as to expose the least number of edges and corners, and to avoid concealed spaces which may be reached readily by flames in case of fire. Heavy timber beams and columns were sized to maintain sufficient strength after exposure to fire and experience has shown these to be much safer for evacuating occupants and fire fighters than many other types of construction. Traditionally, this building typology featured load bearing masonry exterior walls with regular punched windows that combined to provide a durable building enclosure with a useful service life often exceeding one hundred years.
This evolved building typology originally responded to the needs of the Industrial Revolution before the advent of electrification, hence passive measures for daylighting and natural ventilation were privileged in these buildings. Unlike the specialized office, commercial and manufacturing buildings we construct today, the tall wood buildings were mixed use buildings that catered to manufacturing, mercantile and office occupancies that housed a diversity of uses and activities under one roof. Many have since been converted into highly desirable loft condominiums and professional offices, with very few major alterations required, other than subdividing occupancies, replacing windows, restoring wood surfaces, and updating mechanical, electrical and plumbing services.
What "brick and beam" buildings have taught us about sustainable architecture is that it is founded on the 3-Ls: long life (durability, resilience); loose fit (adaptability, flexibility, contingency); and low impact (emissions, ecological footprint). The stock of historical tall-wood buildings in Toronto, as well as many other parts of Canada and the United States, are a living testament to a proven approach that integrated the 3-Ls. Some recent mass timber buildings have largely duplicated the mill building typology because it is highly sought after real estate that is preferred by people over the more conventional modern building types.
There are some critical attributes of mill construction buildings that deserve to be imitated in today's buildings - why be original when we can be good? Innovation does not need to discard proven design strategies and construction techniques when striving for continual improvement. In this regard, an examination of this typology reveals a building DNA that can serve as a benchmark against which today’s designs may be compared.
Most notably:
Regular, rectilinear floor plans and structural grids that are simple and economical to construct;
Post and beam structures with long, clear spans that allow for flexible interior partitioning;
Punched windows that provide vertical segments of non-combustible exterior masonry to receive fire-rated demising walls that enable the fire separation of adjacent occupancies;
The even arrangements of fenestration with large operable openings that promote natural ventilation, daylighting and equitable access to views;
Generous floor-to-floor heights that accommodate suspended mechanical, electrical and plumbing (MEP) services;
Redundant means of vertical access and egress that satisfy fire safety requirements for numerous uses and occupancies;
Robust, low maintenance interior masonry wall surfaces that accommodate a variety of finishes, the addition of thermal insulation and the integration of services;
Raised main floor levels that render a tall inhabitable basement with large windows above grade; and
Single-level concrete foundations that do not encourage automobile use by avoiding underground parking.
But not all aspects of the “brick and beam” buildings were sustainable by today's standards. Using brick as a structural wall material entails a large upfront carbon footprint and the building enclosure is not thermally efficient. Single glazing in steel window frames may have been durable and easy to maintain, but it compromised thermal comfort and increased space conditioning energy demands. To the credit of mill construction buildings, their robust armatures have proven easy to retrofit with the addition of thermal insulation and energy efficient windows. Modern heating, cooling and ventilation systems could be installed with ample headroom for ducts, piping and wiring. The ease of retrofit offered by brick and beam building is unmatched in any other building typology standing today. This typology has been able to gracefully transition from industrial facilities to professional offices and studios, and subsequently to a variety of residential occupancies.
In the life cycle of human settlements and the built environment, this building typology has demonstrated it is sufficiently durable and resilient, such that it can be run down for many decades, after which its robust armature enables revitalization for another cycle of occupancy. This is vital because cities need building stock that can be worn out and devalued so it becomes affordable to communities, such as artists and start-up entrepreneurs, providing a combined live/work/maker space that is eventually gentrified, but only after affordably incubating one or more generations of the creative class.
Built for Lasting Change
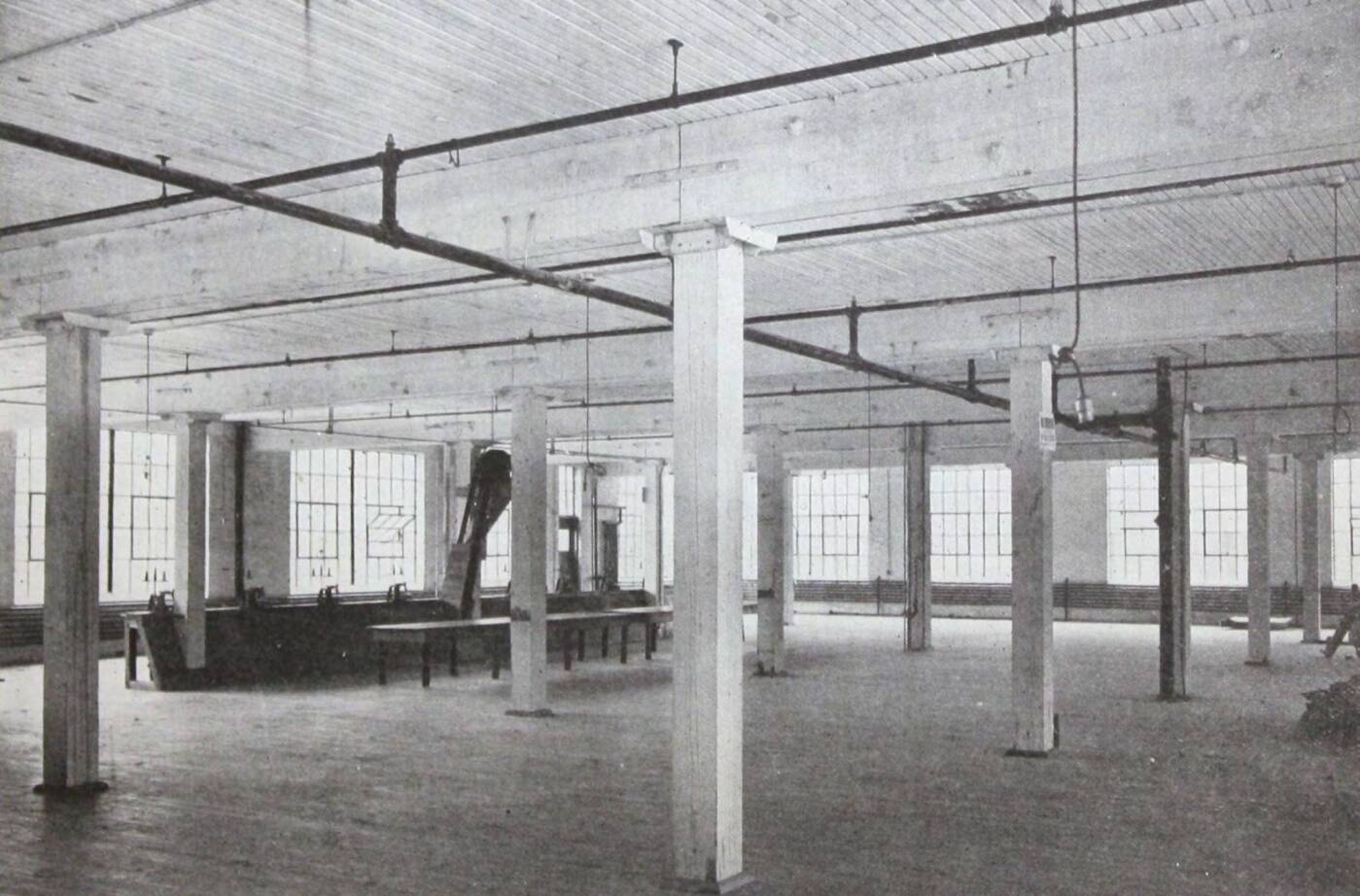
Analysis of the "brick and beam" building typology reveals some interesting relationships. The integration of structure and envelope meant that the building envelope inherited the durability of the structure. An open floor plan coupled to generous height for integrating services and fixtures made for flexible and versatile building facilities. These buildings could be worn down without being worn out, while accommodating multiple uses and occupancies, making them invaluable incubators for industries and crafts. [Source: Heavy Timber Mill Construction Buildings. National Lumber Manufacturers Association, Engineering Bulletin No. 2, May 1916.]
A Typical Historical Tall-Wood Toronto Building
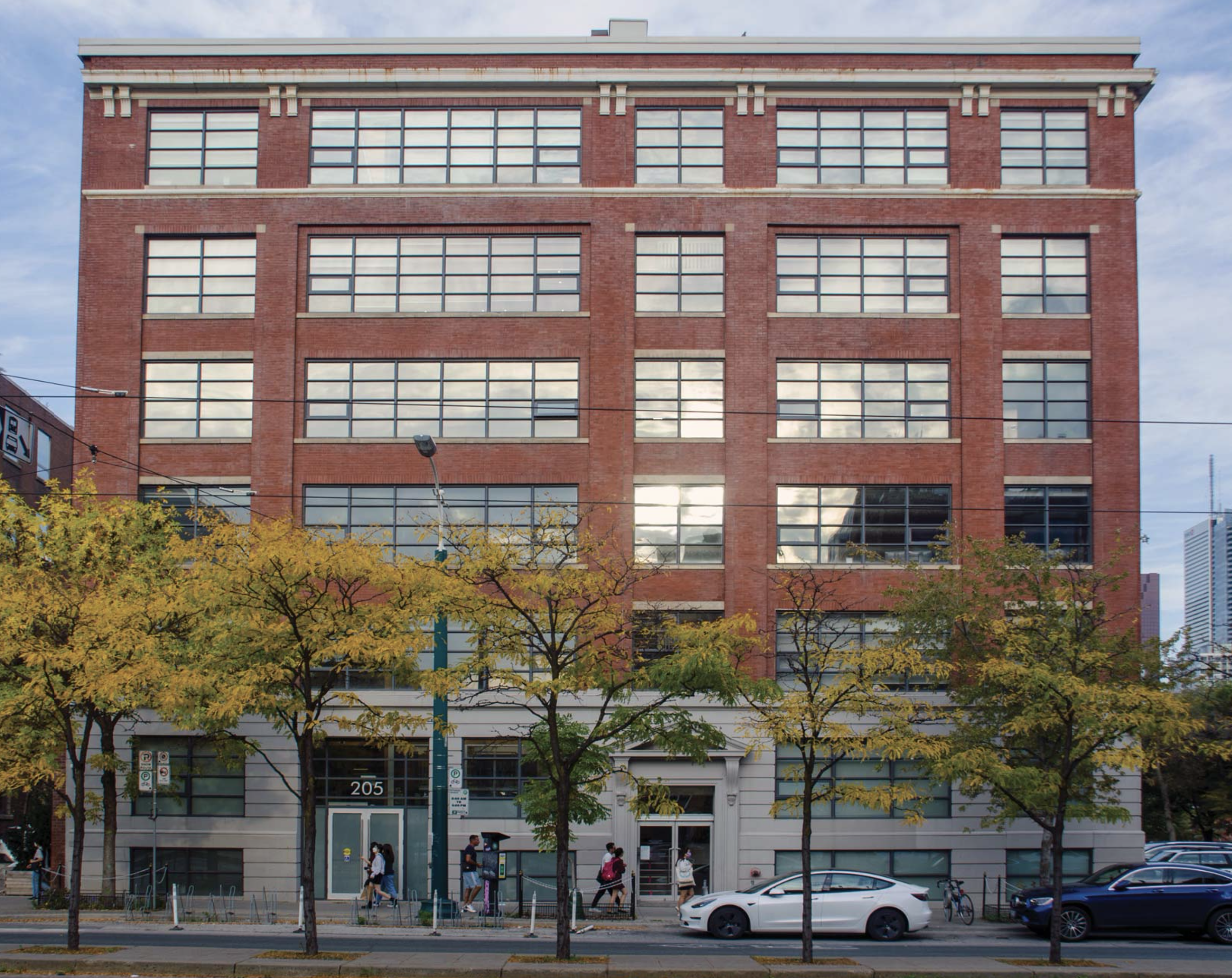
The Empire Clothing Factory, 197-205 Spadina Avenue, Toronto, Ontario was built in 1923, designed by Benjamin Brown, Architect. With over a century of commercial service in Toronto's garment district, this "brick and beam" building continues to house businesses and professional offices. The warm ambience of the interiors and ample daylighting and views on all four facades help maintain competitive rents in what remains a fully occupied income property. [Source: Historical Tall-Wood Toronto by Ross Beardsley Wood, 2024.]
Historical Tall-Wood Toronto is an evidentiary database of late 19th and early 20th century vernacular "brick and beam" buildings that were built using the fire restrictive specifications and methods of heavy timber mill construction in Toronto, Canada. But it is important to recognize this typology was also constructed across many parts of Canada and the United States, and everywhere it was built, it endured.
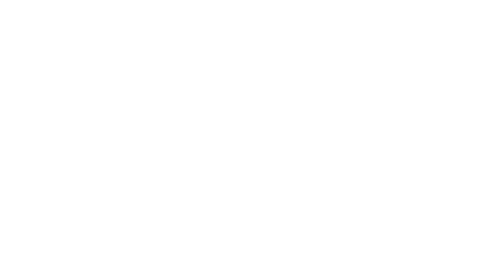
FEATURE
Lessons Learned:
Historical Tall-Wood Toronto
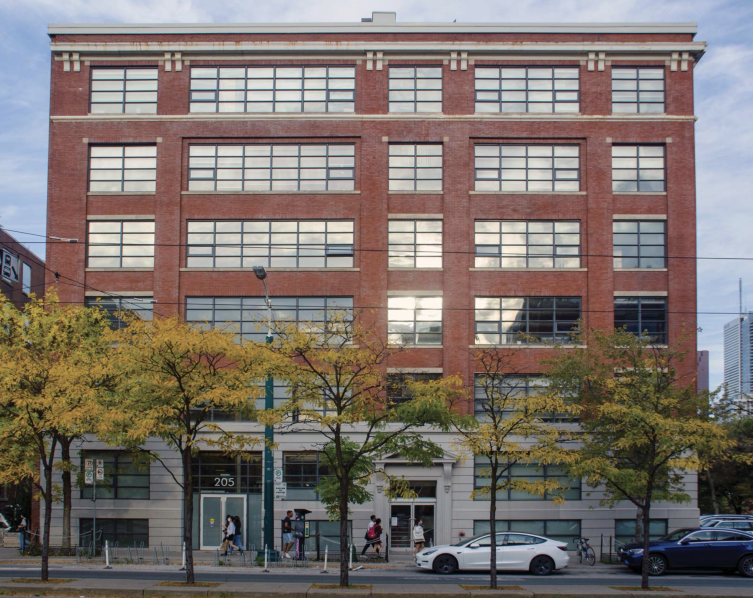
Built for Lasting Change
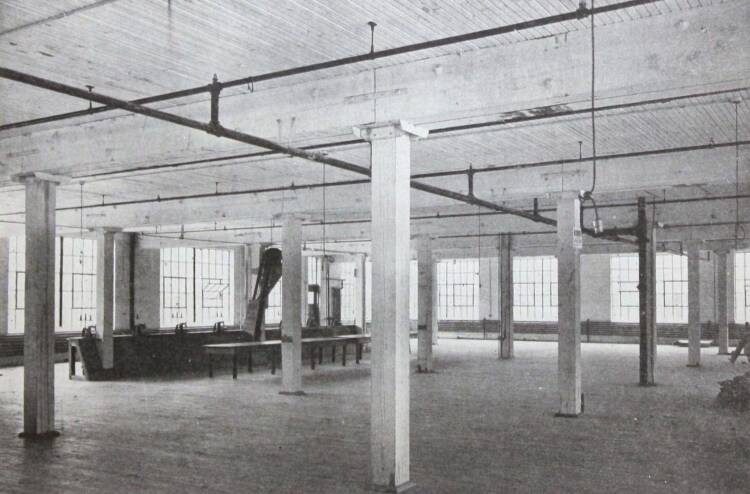
Materials used in the construction sector, such as steel and concrete, generate a significant amount of GHG emissions over their entire lifespan due to the extraction of raw materials, the manufacturing stage, their use and their end-of-life sequence. On the other hand, in addition to having a low carbon footprint, wood generates only a small amount of GHG emissions linked to the harvesting and manufacturing stage. Not only is it capable of storing carbon, but it does so for the entire life of the product.
Wood is one of the few building materials capable of storing carbon over its entire lifespan. Through the process of photosynthesis, trees absorb carbon dioxide (CO2) from the atmosphere and transform it into oxygen (O2). It then uses the carbon (C) in the CO2to form its material (wood), enabling it to grow. In general, it is estimated that 1 m3 of wood sequesters just under 1 tonne of CO2. Once mature, the tree grows at a slower rate and stores less carbon. After 75 to 120 years of life, trees will eventually die and decompose naturally, aided by fungi and/or insects, or sooner if burned in a forest fire.
In this way, much of the carbon accumulated during its life will be returned to the atmosphere in the form of CO2, thereby completing the forest carbon cycle. The harvested tree is replaced by a younger one, thus starting a new cycle of carbon sequestration cycle. By using wood as a building material, we delay the moment when this carbon is released or re-emitted into the atmosphere. Therefore, it is possible to extend forest carbon sequestration beyond the life of the tree by using it as a building material.
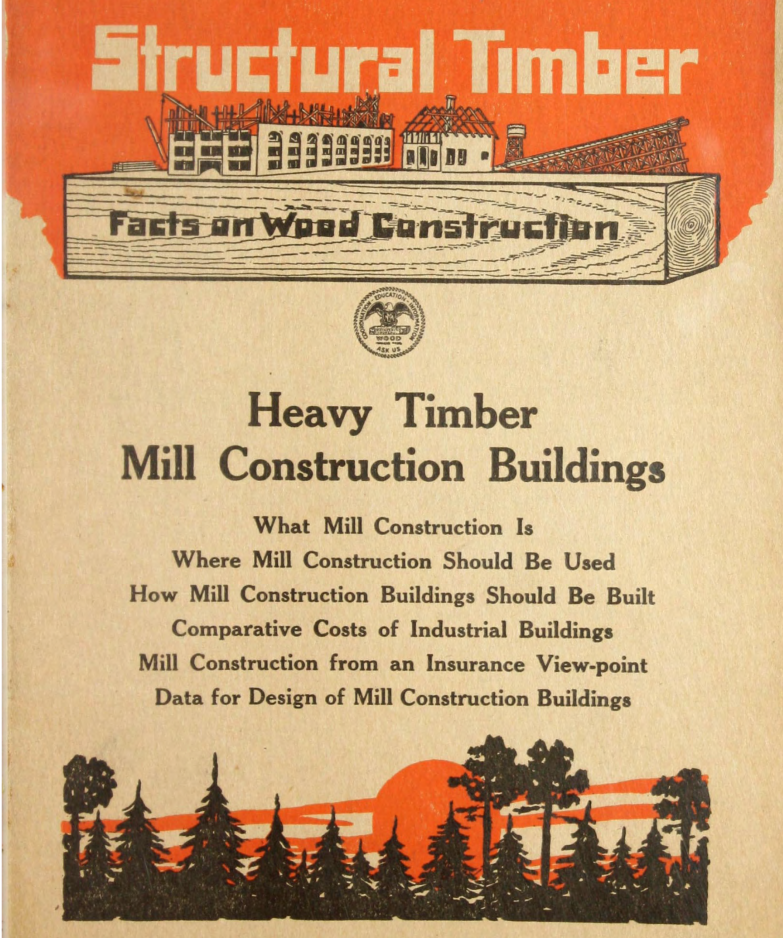
Heavy Timber Mill Construction
In the same way that light wood-frame house construction evolved into prescriptive codes and standards, mill construction pointed the way to the future of mass timber buildings whereby a series of formulaic design guidelines for common building archetypes would eliminate the need for alternative solutions to demonstrate code compliance. Complementary innovations in prefabricated modular building envelopes would enable rapid installation and subsequently, the periodic maintenance, retrofit and eventual replacement of enclosures over the building life cycle. Design for economy, efficiency, durability, flexibility/adaptability, resilience and low whole life carbon are key to the future of sustainable architecture. Our heritage "brick and beam" buildings did much of the heavy lifting needed to develop a contemporary sustainability framework for buildings crafted from wood.
This publication about Historical Tall Wood Toronto catalogues a cohort of such buildings that have endured and, in many ways, outperformed the vast majority of 20th and 21st century architecture. But this achievement can only be appreciated by taking the long view and considering the life cycle of buildings - the sort of design thinking that was baked into our historical tall-wood buildings, lessons learned that we must rediscover.
The term "mill construction" describes a type of building construction where interior framing and floors are of timber, arranged in heavy solid masses, and smooth flat surfaces, so as to expose the least number of edges and corners, and to avoid concealed spaces which may be reached readily by flames in case of fire. Heavy timber beams and columns were sized to maintain sufficient strength after exposure to fire and experience has shown these to be much safer for evacuating occupants and fire fighters than many other types of construction. Traditionally, this building typology featured load bearing masonry exterior walls with regular punched windows that combined to provide a durable building enclosure with a useful service life often exceeding one hundred years.
This evolved building typology originally responded to the needs of the Industrial Revolution before the advent of electrification, hence passive measures for daylighting and natural ventilation were privileged in these buildings. Unlike the specialized office, commercial and manufacturing buildings we construct today, the tall wood buildings were mixed use buildings that catered to manufacturing, mercantile and office occupancies that housed a diversity of uses and activities under one roof. Many have since been converted into highly desirable loft condominiums and professional offices, with very few major alterations required, other than subdividing occupancies, replacing windows, restoring wood surfaces, and updating mechanical, electrical and plumbing services.
What "brick and beam" buildings have taught us about sustainable architecture is that it is founded on the 3-Ls: long life (durability, resilience); loose fit (adaptability, flexibility, contingency); and low impact (emissions, ecological footprint). The stock of historical tall-wood buildings in Toronto, as well as many other parts of Canada and the United States, are a living testament to a proven approach that integrated the 3-Ls. Some recent mass timber buildings have largely duplicated the mill building typology because it is highly sought after real estate that is preferred by people over the more conventional modern building types.
There are some critical attributes of mill construction buildings that deserve to be imitated in today's buildings - why be original when we can be good? Innovation does not need to discard proven design strategies and construction techniques when striving for continual improvement. In this regard, an examination of this typology reveals a building DNA that can serve as a benchmark against which today’s designs may be compared.
Most notably:
Regular, rectilinear floor plans and structural grids that are simple and economical to construct;
Post and beam structures with long, clear spans that allow for flexible interior partitioning;
Punched windows that provide vertical segments of non-combustible exterior masonry to receive fire-rated demising walls that enable the fire separation of adjacent occupancies;
The even arrangements of fenestration with large operable openings that promote natural ventilation, daylighting and equitable access to views;
Generous floor-to-floor heights that accommodate suspended mechanical, electrical and plumbing (MEP) services;
Redundant means of vertical access and egress that satisfy fire safety requirements for numerous uses and occupancies;
Robust, low maintenance interior masonry wall surfaces that accommodate a variety of finishes, the addition of thermal insulation and the integration of services;
Raised main floor levels that render a tall inhabitable basement with large windows above grade; and
Single-level concrete foundations that do not encourage automobile use by avoiding underground parking.
But not all aspects of the “brick and beam” buildings were sustainable by today's standards. Using brick as a structural wall material entails a large upfront carbon footprint and the building enclosure is not thermally efficient. Single glazing in steel window frames may have been durable and easy to maintain, but it compromised thermal comfort and increased space conditioning energy demands. To the credit of mill construction buildings, their robust armatures have proven easy to retrofit with the addition of thermal insulation and energy efficient windows. Modern heating, cooling and ventilation systems could be installed with ample headroom for ducts, piping and wiring. The ease of retrofit offered by brick and beam building is unmatched in any other building typology standing today. This typology has been able to gracefully transition from industrial facilities to professional offices and studios, and subsequently to a variety of residential occupancies.
In the life cycle of human settlements and the built environment, this building typology has demonstrated it is sufficiently durable and resilient, such that it can be run down for many decades, after which its robust armature enables revitalization for another cycle of occupancy. This is vital because cities need building stock that can be worn out and devalued so it becomes affordable to communities, such as artists and start-up entrepreneurs, providing a combined live/work/maker space that is eventually gentrified, but only after affordably incubating one or more generations of the creative class.
Humans have been building with wood since devising their earliest forms of primitive shelter. Unlike stone, wood proved a far more workable material that could be assembled by individual or small groups of workers. While it did not produce monumental architecture, it also did not demand decades of labour by a vast workforce. Quick and easy to construct, wood buildings proved to be durable and resilient while offering warmth and natural beauty. From the earliest European settlements to this day in Canada, wood accounts for most of our housing, and more recently we have witnessed the introduction of mass timber buildings that deploy a diverse palette of engineered wood products. It is predicted that a sustainable built environment will be founded on buildings that are constituted from an even higher proportion of bio-based materials than we use in conventional construction today, hence much of Canada's promise and destiny will continue to depend on her forests and the wood products they produce.
With our environment in mind, the advance of the contemporary "green" building movement continues to evolve, but a new vernacular of 21st century architecture with a sustainable ecological footprint has yet to fully emerge. While we seek to fashion reliable and robust recipes for our everyday buildings, ranging from apartments and stores, to schools and offices, there is much to learn from the resilient and adaptable warehouse and light-factory buildings that line the streets of Canada’s historic manufacturing districts.