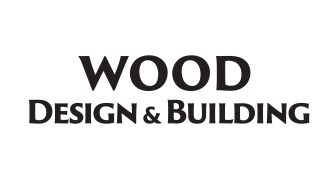
ASK AN EXPERT
Shrinkage Limits
for Multi-Storey Wood-Framed Buildings
I’m an engineer working on a five-storey wooden building. Are there any defined shrinkage limits for the materials?
While there are no specific shrinkage limits of wood members cited in NBC2020 or CSA O86, in mid-rise (5- or 6-storey) wood-framed buildings, it’s essential that the design accounts for the expected range of motion as the totals become cumulative and can lead to structural issues.
Shrinkage – and swelling – is of particular concern when wood is combined with other materials and systems, such as around reinforced concrete elevator shafts and plumbing lines, which will not move while the wood framing or members around them shift. You should also factor in that some materials, such as steel beams and PVC piping, can expand or contract due to temperature changes. Free best-practice guides are available in the CWC resource hub, which provide examples of details such as transitions from elevator shafts into light-frame systems.
Cutting oversized openings for mechanical, electrical, and plumbing (MEP) systems allows for movement, but the holes can’t impact the structural strength of the members and must be within the limits of CSA O86 for lumber beams or the manufacturer’s recommendations for engineered wood products (EWP). Another option is to use expansion or slip joint connectors.
Shrinkage parallel-to-grain is a relatively minor concern and is only relevant to check for cumulative effects across the entire height of the building. Perpendicular-to-grain shrinkage is roughly 40 times higher and is relevant to the whole building and local-member scales. This is especially true with larger-sized members with metal connections or contact with other systems. In either case, the engineer will need to make sure the dimensional allowances can accommodate for any movements due to the wood reaching the equilibrium moisture content.
There are shrinkage calculators available online that factor in details such as species, moisture content, and grain orientation of the materials used, as well as detailed project specs. The CWC website has its own online dimension calculator for single members or light-wood-frame walls.
You can minimize the amount of wood movement after construction by selecting products with the lowest possible moisture content. For dimensional lumber, use products that are kiln dried (“KD”) or surface dry (“S-Dry”) as they will have a moisture content of 19% or less. Glulam products have a moisture content between 11 and 15%, while engineered products such as I-joints typically range from 6 to 12% moisture content. To minimize any differential in expansion or shrinkage, use materials with similar moisture properties for connected floor systems or other structural components.
Protect the components from exposure to rain or other sources of moisture prior to installation and enclose the structure to protect the materials from the elements as soon as possible after installation.
How can one determine the Fire Resistance Rating (FRR) and Sound Transmission Coefficient (STC) ratings for wood stud shear walls that include plywood on one or both sides and are finished with gypsum? To achieve a 1-hour rating, is it possible to use an existing tested gypsum assembly to meet both FRR and STC requirements and simply add plywood without affecting the ratings? Is there a better way to determine the FRR and STC ratings in this scenario?
ASK AN EXPERT
Prolonging the Life of Wood Products with Pressure Treatment
How long will pressure treated wood last in a damp environment, and what can I do to prolong its lifespan?
As with any building material, longevity is dependent on factors such as proper specification, installation and maintenance. From your home’s foundation to the transportation of goods/passengers, to the delivery of electricity – pressure treated wood products are reliable because they last. In fact, service lives of treated wood fence posts have been documented to last more than 60 years.
Click to view resources on pressure-treated wood from CWC
Treatment Process
In a typical pressure treatment process, wood is place in a large horizontal cylinder. The preservative solution is introduced into the cylinder and is forced into the wood through cycles of vacuum and pressure. This forms a protective envelope of preservative protection in the wood. Preservatives protect the wood from attack by wood ingesting insects, such as termites, and wood rot caused by fundal decay. The pressure treatment process is an effective method to extend the service life of wood products. The Canadian Wood Council and Wood Preservation Canada have collaborated on several info sheets and specification guides, freely available in the CWC resource hub.
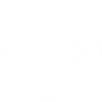
For more information about pressure treated wood, please visit www.woodpreservation.ca.
Field Treatment – End Cut Preservatives
Wood is made-up of a combination of sapwood and heartwood. Sapwood is the living, outer portion of a log and heartwood is the dead, inner wood. Typically, the sapwood of most species is receptive to wood preservative penetration whereas the heartwood is not. This is why, when building outdoor projects with pressure treated wood, it is important to protect the cut ends, large drill holes, and other field cuts. Cutting or drilling into pressure treated wood has the potential to expose portions of the sapwood that are untreated with preservative. Two coats of a brush on end cut wood preservative should be applied to all dry saw cuts, large drill holes and other field cuts at the time of construction.
There are two field treatment preservatives specified in the CSA O80 standard that can be used for cut ends/field cuts in both above ground and ground contact applications:
1. Creosote, a distillate derived from tar by carbonization of bituminous coal and meets AWPA P1/P13
2. Copper naphthenate, a solvent that meets AWPA P36 and contains Copper (present as Copper Naphthenate) 2%
Fasteners and Hardware
Connectors
Connectors used for ACQ, CA, CCA or MCA pressure treated wood must be manufactured from steel and be either hot-dip galvanized in accordance with ASTM A653, G185 designation, or hot-dipped galvanized after manufacture in accordance with ASTM A123. Stainless steel connectors (type 304 or 316) are recommended for maximum service life and/or severe applications.
Pressure treated wood products should not be in direct contact with untreated wood or exposed to conditions under which the material could reasonably be expected to be colonized by mycelial growth of fungus directly from soil or via moisture wicking building materials.
Fasteners
Fasteners for ACQ, CA, CCA or MCA pressure treated wood must be hot-dipped galvanized in accordance with ASTM A153. Stainless steel should be used for maximum service life and/or severe applications. Where appropriate, copper fasteners may also be used. Fasteners used in combination with metal connectors must be the same type of metal to avoid galvanic corrosion caused by dissimilar metals. For example: stainless steel fasteners should not be used in combination with galvanized connectors.


ASK AN EXPERT
Shrinkage Limits
for Multi-Storey Wood-Framed Buildings
I’m an engineer working on a five-storey wooden building. Are there any defined shrinkage limits for the materials?
While there are no specific shrinkage limits of wood members cited in NBC2020 or CSA O86, in mid-rise (5- or 6-storey) wood-framed buildings, it’s essential that the design accounts for the expected range of motion as the totals become cumulative and can lead to structural issues.
Shrinkage – and swelling – is of particular concern when wood is combined with other materials and systems, such as around reinforced concrete elevator shafts and plumbing lines, which will not move while the wood framing or members around them shift. You should also factor in that some materials, such as steel beams and PVC piping, can expand or contract due to temperature changes. Free best-practice guides are available in the CWC resource hub, which provide examples of details such as transitions from elevator shafts into light-frame systems.
Cutting oversized openings for mechanical, electrical, and plumbing (MEP) systems allows for movement, but the holes can’t impact the structural strength of the members and must be within the limits of CSA O86 for lumber beams or the manufacturer’s recommendations for engineered wood products (EWP). Another option is to use expansion or slip joint connectors.
Shrinkage parallel-to-grain is a relatively minor concern and is only relevant to check for cumulative effects across the entire height of the building. Perpendicular-to-grain shrinkage is roughly 40 times higher and is relevant to the whole building and local-member scales. This is especially true with larger-sized members with metal connections or contact with other systems. In either case, the engineer will need to make sure the dimensional allowances can accommodate for any movements due to the wood reaching the equilibrium moisture content.
There are shrinkage calculators available online that factor in details such as species, moisture content, and grain orientation of the materials used, as well as detailed project specs. The CWC website has its own online dimension calculator for single members or light-wood-frame walls.
You can minimize the amount of wood movement after construction by selecting products with the lowest possible moisture content. For dimensional lumber, use products that are kiln dried (“KD”) or surface dry (“S-Dry”) as they will have a moisture content of 19% or less. Glulam products have a moisture content between 11 and 15%, while engineered products such as I-joints typically range from 6 to 12% moisture content. To minimize any differential in expansion or shrinkage, use materials with similar moisture properties for connected floor systems or other structural components.
Protect the components from exposure to rain or other sources of moisture prior to installation and enclose the structure to protect the materials from the elements as soon as possible after installation.
Prolonging the Life of Wood Products with Pressure Treatment
Depending on the type of preservative used, application, and climate, treated wood can last an extremely long time. In fact, service lives of treated fence posts have been documented to last more than 60 years. That said, site conditions and installation errors can significantly shorten the lifespan.
Click to view resources on pressure-treated wood from CWC
How long will pressure-treated wood last in a damp environment, and what can I do to prolong its lifespan?
Treatment Process
In a typical pressure treatment process, wood is place in a large horizontal cylinder. The preservative solution is introduced into the cylinder and is forced into the wood through cycles of vacuum and pressure. This forms a protective envelope of preservative protection in the wood. Preservatives protect the wood from attack by wood ingesting insects, such as termites, and wood rot caused by fundal decay. The pressure treatment process is an effective method to extend the service life of wood products. The Canadian Wood Council and Wood Preservation Canada have collaborated on several info sheets and specification guides, freely available in the CWC resource hub.
ASK AN EXPERT
Field Treatment – End Cut Preservatives
Wood is made-up of a combination of sapwood and heartwood. Sapwood is the living, outer portion of a log and heartwood is the dead, inner wood. Typically, the sapwood of most species is receptive to wood preservative penetration whereas the heartwood is not. This is why, when building outdoor projects with pressure treated wood, it is important to protect the cut ends, large drill holes, and other field cuts. Cutting or drilling into pressure treated wood has the potential to expose portions of the sapwood that are untreated with preservative. Two coats of a brush on end cut wood preservative should be applied to all dry saw cuts, large drill holes and other field cuts at the time of construction.
There are two field treatment preservatives specified in the CSA O80 standard that can be used for cut ends/field cuts in both above ground and ground contact applications:
1. Creosote, a distillate derived from tar by carbonization of bituminous coal and meets AWPA P1/P13
2. Copper naphthenate, a solvent that meets AWPA P36 and contains Copper (present as Copper Naphthenate) 2%
Fasteners and Hardware
Connectors
Connectors used for ACQ, CA, CCA or MCA pressure treated wood must be manufactured from steel and be either hot-dip galvanized in accordance with ASTM A653, G185 designation, or hot-dipped galvanized after manufacture in accordance with ASTM A123. Stainless steel connectors (type 304 or 316) are recommended for maximum service life and/or severe applications.
Pressure treated wood products should not be in direct contact with untreated wood or exposed to conditions under which the material could reasonably be expected to be colonized by mycelial growth of fungus directly from soil or via moisture wicking building materials.
Fasteners
Fasteners for ACQ, CA, CCA or MCA pressure treated wood must be hot-dipped galvanized in accordance with ASTM A153. Stainless steel should be used for maximum service life and/or severe applications. Where appropriate, copper fasteners may also be used. Fasteners used in combination with metal connectors must be the same type of metal to avoid galvanic corrosion caused by dissimilar metals. For example: stainless steel fasteners should not be used in combination with galvanized connectors.
A: