In response to climate challenges and energy efficiency requirements, we must acknowledge the urgent need for the construction industry to transition to bio-based materials as a solution to reduce our collective carbon footprint. Among these solutions, wood fibre insulation stands out given its interesting technical properties, particularly its thermal performance, humidity control and low carbon footprint. However, integrating wood fibre insulation in the Canadian context remains a challenge requiring regulatory changes and technical adaptations.
The new addition to the École des Cerisiers, which constitutes a mass-timber project of 2384 m2, demonstrates the potential of wood fibre insulation in the building envelope. This project combines innovation and sustainability by integrating bio-based materials in both the structure and in the building envelope.
Des Cerisiers primary school is situated in the centre of municipality of Maskinongé, where it serves a community characterized by its agricultural background, the solidarity of its 2300 inhabitants, and its strong community engagement. The project revitalizes the existing school, enabling it to host all the town’s students under the same roof. This project is the only extension project resulting from the province-wide Lab-École design competition. In this unique initiative, and in close collaboration with the local school team, the program was designed to accurately reflect the specific needs and values of the region.
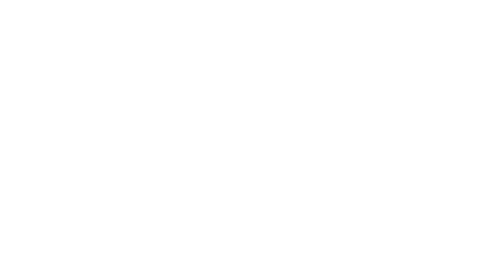
FEATURE
Integrating wood fibre insulation at École des Cerisiers: a case study
Scroll to Read
From details to the construction site
Step 1: studying the performance and technical properties of the components of the building envelope
Using wood fibre insulation is not an innovative practice per se, as the insulation is manufactured from offcuts from the timber industry. However, what constitutes the innovation of this project is the use of this insulation on a large-scale project in the context of a Canadian climate.
Two processes are used to manufacture wood fibre insulation: wet and dry. In the wet process, wood fibres are mixed with water and sometimes with a binding agent, and the mix is then mechanically compressed and dried. In the dry process, wood fibres are sprayed with paraffin, dried using warm air, and then treated with a polyurethane resin. Some dry processes also require the binding agent to be hardened through exposure air and water vapour.
Based on our research, it appears that insulation panels manufactured using a dry process are more suitable for our projet. In addition, the range of panel thicknesses available through a dry process allows us to achieve our thermal performance targets without laminating several panels. Despite the numerous manufacturers of bio-based insulation operating in Québec, none currently use a dry fabrication process.
Managing humidity and dew point
Using wood-based insulation in the building envelope requires extreme caution in managing water vapour and condensation: seasonal fluctuations in temperature in Québec may cause a corresponding movement of the dew point within the thickness of the envelope. The location of the vapour barrier may consequently be effective only for part of the year, but risk condensation within the insulation in the other part of the year. Migration, retention or dew point in a bio-based component may lead to fungal growth or loss of thermal and airtightness performance.
To achieve effective airtightness and reduce condensation risks in the building envelope, it was necessary to develop an assembly with two membranes: a weather barrier to protect wood components against wind and external water sources, and a vapour barrier to protect against humidity from inside the building. Given the mass timber structure and timber frame studs, the assembly of the building envelope needs air, vapour, and thermal control layers which are permeable to vapour diffusion to prevent rotting. This is even more important when the wall cavities are filled with batt insulation.
Some insulation, such as mineral wool, glass fibre and wood fibre, allow such vapour diffusion, unlike plastic foams and polystyrene. Multitherm panels and Gutex Thermoflex batt insulation have similar permeability to mineral wool products. However, it is difficult to compare data since Gutex products have not yet been tested under the ASTM E96 standard on “Standard Test Methods for Water Vapour Transmission of Materials”.
Intelligent membranes, such as Pro Clima Intello X vapour barrier, adjust permeability based on changes in humidity. In winter, they become more resistant to diffusion to prevent inside humidity from seeping into the wall and towards the exterior, while in summer, they become more permeable to diffusion and allows humid air to evacuate more efficiently, thus promoting drying. Pro Clima Solitex Mento 1000 weather barrier membrane has high vapour permeability allowing humidity in the assembly to evacuate towards the exterior.
Fire resistance of wood fibre insulation
One of the major challenges was the issue of standards and certifications. At present, the majority of wood fibre products are manufactured in Europe and are not fully certified in compliance with North American standards and testing methods.
No wood fibre insulation currently on the market seems to successfully pass the CAN/ULC S114 non-combustibility tests. However, the Gutex Multitherm panel was tested for the flame spread index and smoke developed index in compliance with ASTM E84 and CAN/ULC-S-102. For the ASTM E84 standard, the panel was classified as class B with a flame spread index (FSI) of 65 and smoke developed index (SDI).
No non-combustibility testing or testing for the flame spread index and smoke developed index in compliance with North American standards appears to have been carried out on Gutex Thermoflex mattress insulation. This means that using such insulation in non-combustible walls or fire resistant walls may be compromised as the makeup of building faces must comply with Table 3.2.3.7 “Minimum Construction Requirements for Exposing Building Faces”.
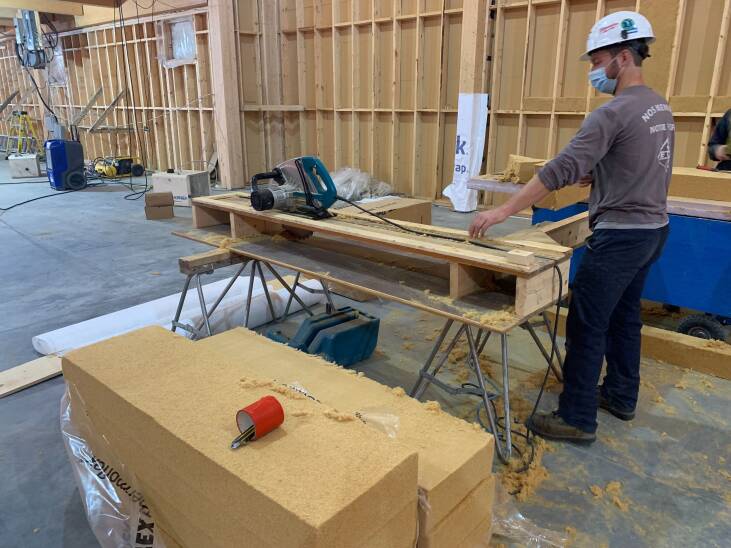
The integration of wood fibre insulation into the building envelope was carried out in three steps: (1) theoretical assessment of the performance and technical properties of the assembly components, (2) comparative analysis against a traditional synthetic and non-bio-based assembly and (3) the development of the building envelope details.
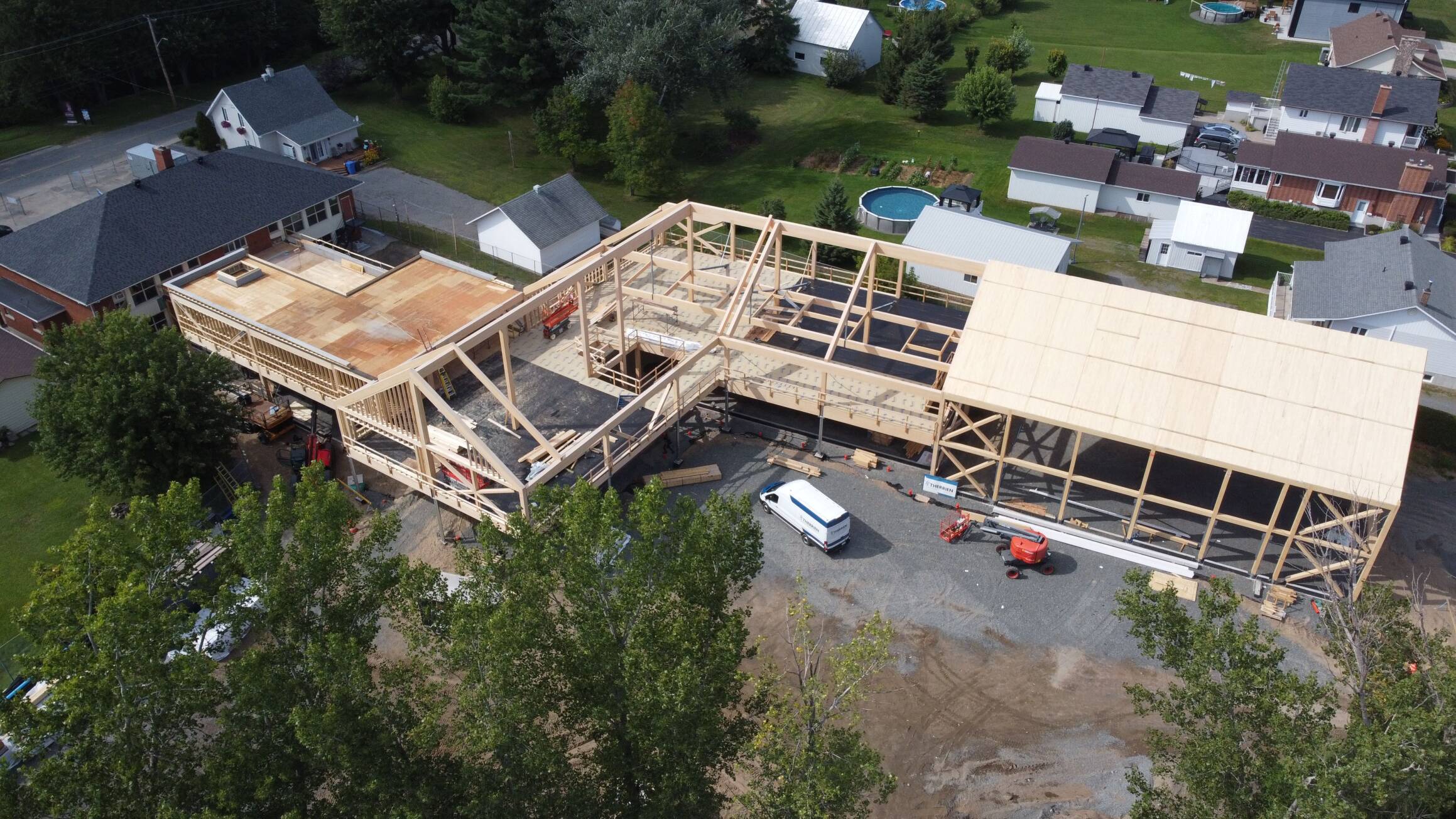
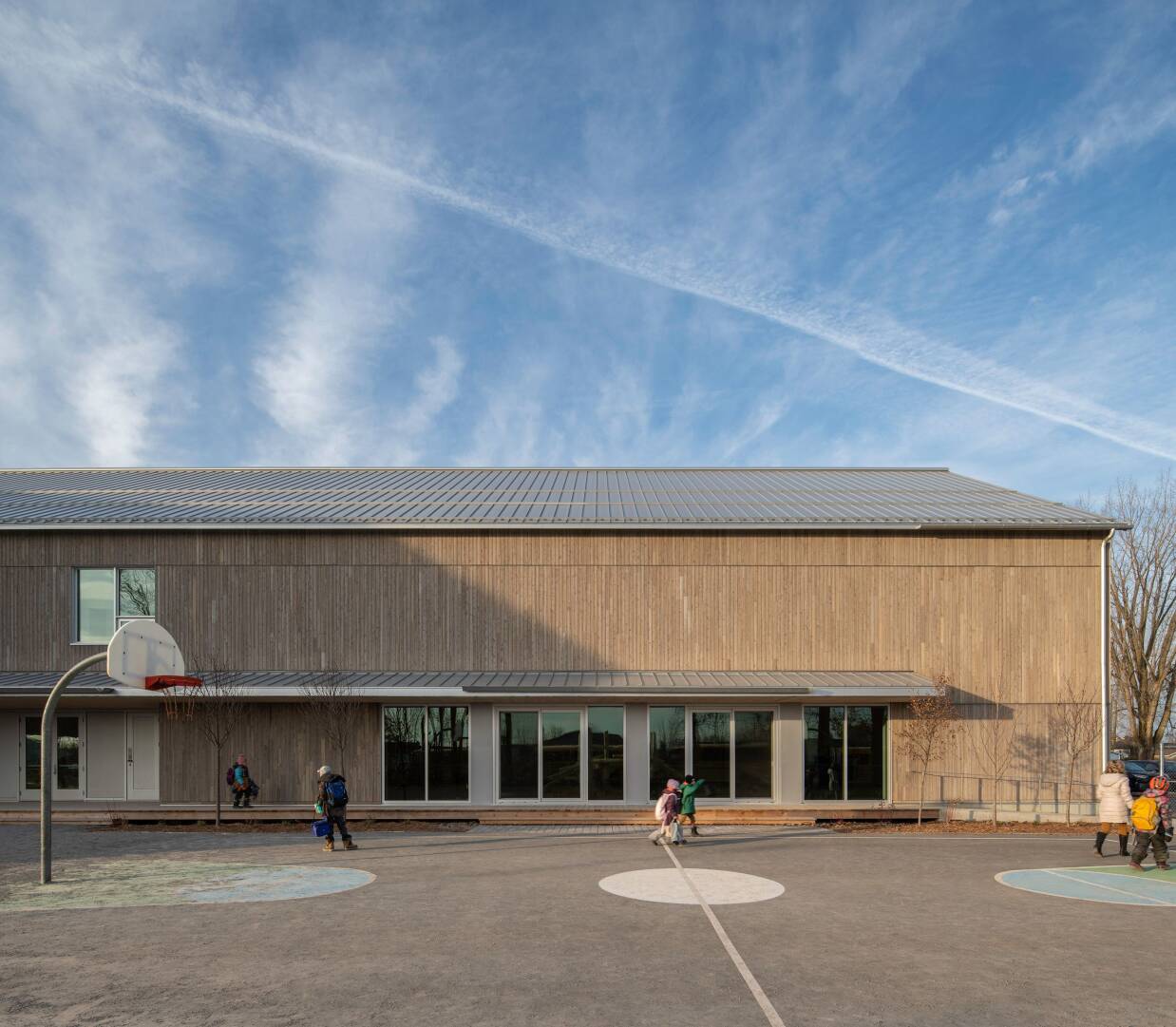
Step 3: Detailing the building envelope
Following an analysis of the product data sheets and examples of typical details from the manufacturer, we analyzed the critical envelope details in collaboration with the building envelope consultant.
The typical details covered by the study are:
Junction of the exterior wall with the foundation (sectional view)
Junction of the exterior wall with a window (sectional view and plan view)
Junction of the exterior wall with a curtain wall (sectional view and plan view)
Junction of the exterior wall with the different roof compositions
Junction of the exterior wall with the soffit and awning
Details of the ventilated (sloped) roof to reduce thermal bridges
Step 2: Comparative analysis against non-bio-based assemblies
Wood fibre panels are an interesting alternative to plastic foam insulation and even mineral wool insulation, as the rigid panels have comparable properties to the reference products. Since an air or weather barrier can be applied directly to the panels, the use of rigid panels also allows the elimination of a backing panel (in gypsum or plywood) from the composition.
In our preliminary analysis, we selected comparable parameters for the reference system (excluding bio-based insulation) and the proposed system (including bio-based insulation). Water vapour permeability, thermal performance, and installation methods were assessed in each of the systems to ensure a fair comparison.
In our typical institutional projects, three types of insulation are used in buildings: (1) rigid insulation for the roof, (2) semi-rigid insulation behind the rain screen and (3) batt insulation between the wood stud cavities in the walls and partitions. In order to evaluate as many products as possible in this case study, we did a comparative study of the thermal performances for all three types of insulation. However, in the built project, two of these three studied elements were retained and incorporated - only the rigid wood-fibre insulation for the roof was not used due to budgetary and technical reasons.
Photographer: Taillefer + Paquet + Leclerc Architectes consortium
Photographer: David Boyer
Photographer: David Boyer
Photographer: David Boyer
Photographer: David Boyer
Photographer: David Boyer
Photographer: David Boyer
Photographer: Maxime Brouillet
Photographer: Maxime Brouillet
Photographer: Maxime Brouillet
How to ensure compliance with the procurement rules laid down by the Secrétariat du Conseil du Trésor (Québec) for a public project?
The procurement rules around public tenders led us to revise sections of our specification regarding the components of the building envelope. Acceptable products must operate as part of an overall system rather than as individual products, and we ensured compatibility between components through our communications with suppliers. Risks relating to product sourcing, the associated budgetary risks, and technical constraints were also assessed.
How to document the use of wood fibre insulation and its impact on the performance of the building envelope?
Given that the use of wood fibre insulation is relatively unknown amongst the project team, it was essential for us and our stakeholders to find a way to document and collect real-time data of the envelope’s performance after construction. To deepen the scope and improve the accuracy of this analysis, we decided to collaborate with a building envelope consultant, Envelop3. They assisted us with documenting the performance of the built envelope via a series of on-site tests. These tests allowed us to measure the impact of the wood fibre insulation on the building’s energy efficiency.
Why would an institutional client take the risk of using wood fibre insulation in the building envelope?
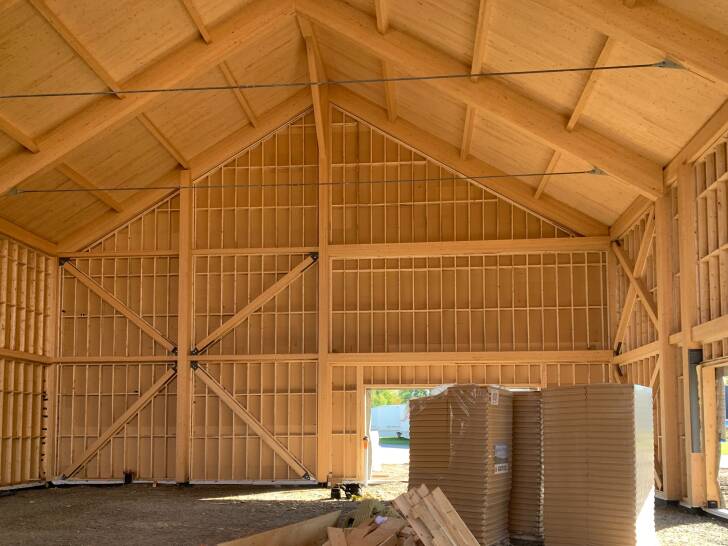
Photographer: David Boyer
Photographer: Taillefer + Paquet + Leclerc Architectes consortium
Photographer: Taillefer + Paquet + Leclerc Architectes consortium
By Elaine Tat and Thomas Gauvin-Brodeur
Prospects for the construction industry
The results of on-site testing will allow us to expand and contribute to the database on the performance of wood fibre insulation in building the envelope, specifically adapted to the Québec climate.
In addition to the report on quantifying GHG emissions of construction materials, the project highlights low-carbon options for building assemblies without compromising their energy efficiency. These alternatives to synthetic and non-bio-based materials offer considerable potential for the transition to more sustainable and resilient buildings.
This project forms part of a wider approach aimed at promoting and developing the bio-based insulation industry in Québec and Canada. The wood fibre insulation used in this project had to be imported from Europe, given the lack of equivalencies on the Canadian and Québec markets. This situation highlights the importance of diversifying and reinforcing a local industry, in particular by upcycling waste from the wood processing industry. By encouraging the development and manufacturing of bio-based insulation in Québec, it will be possible to respond to a rapidly growing demand, reduce reliance on imported materials and promote a circular and local economy.
Ultimately, this new school addition embodies a project where innovation and sustainability are core values. Bio-based products are just as seamless to integrate and perform just as effectively as the synthetic systems widely used in the industry. It’s a powerful reminder that even in public institutional projects, sustainability and innovation can go hand in hand.
Architects: Leclerc architectes + Lucie Paquet + Paulette Taillefer
Engineering: Stantec
Landscape architect: Mousse Architecture de Paysage
Enveloppe consultant: Envelop3
General contractor: Therrien Entrepreneur Général
Client: Centre de services scolaire du Chemin-du-Roy
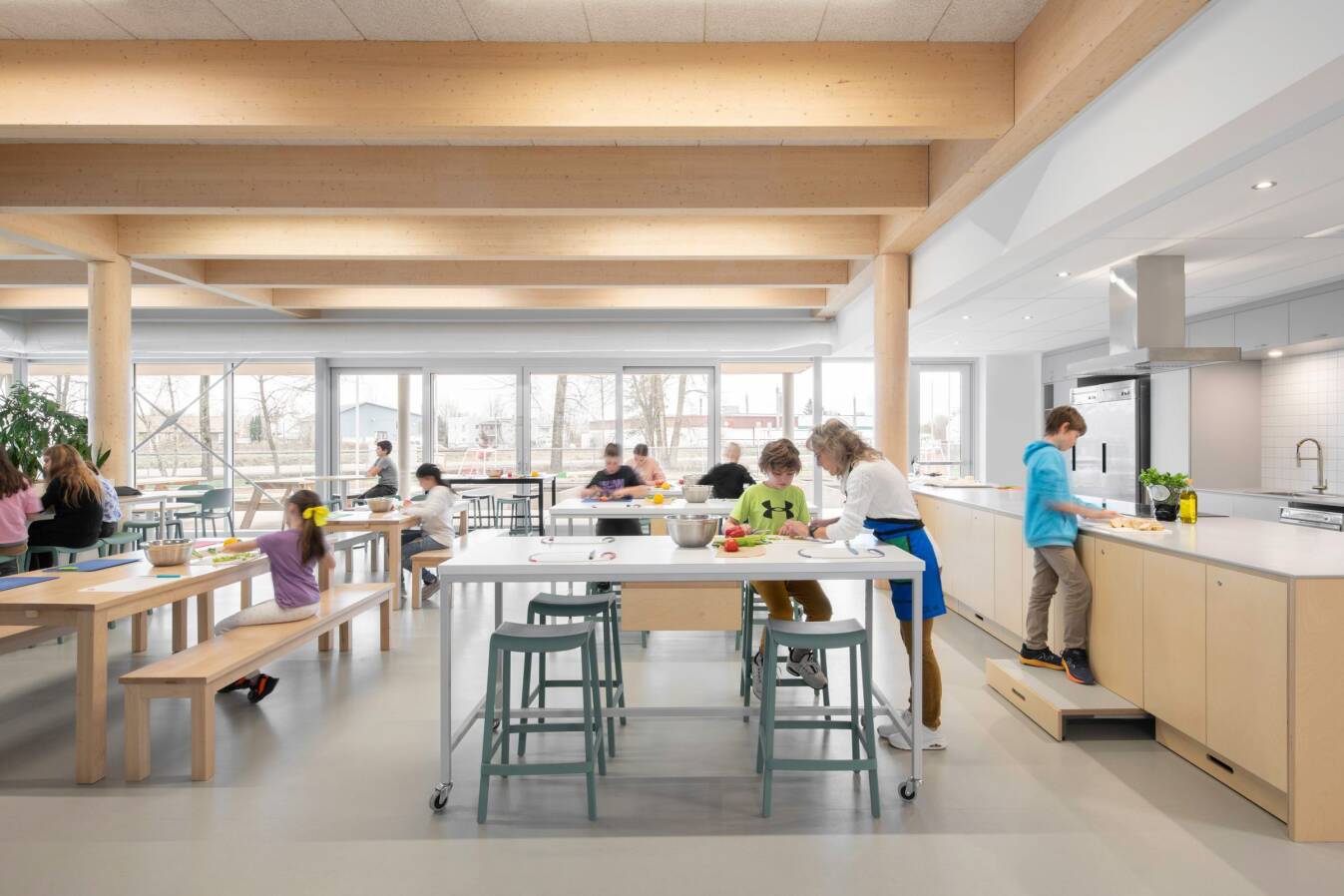
Challenges in the context of publicly funded projects
In 2015, the Government of Québec adopted a policy on integrating wood in construction to encourage the industry to increase the use of wood in public buildings, promote sustainable development, support the local economy and reduce the construction sector’s carbon footprint.
As architects and designers, we have an opportunity to contribute to these objectives by advocating for the integration of wood-based materials in building envelope assemblies as well as in exterior or interior finishes. The use of wood fibre insulation has so far prompted interest from several stakeholders, as well as members from the industry at large, who were excited and willing to collaborate on its integration to a public project.
This project benefited from additional financial support in the form of a subsidy from the Ministère des Ressources naturelles et des Forêts (MRNF) and the backing of the municipality of Maskinongé, which demonstrates a concrete commitment to increasing the integration of wood in construction.
An innovative project at the heart of an engaged community
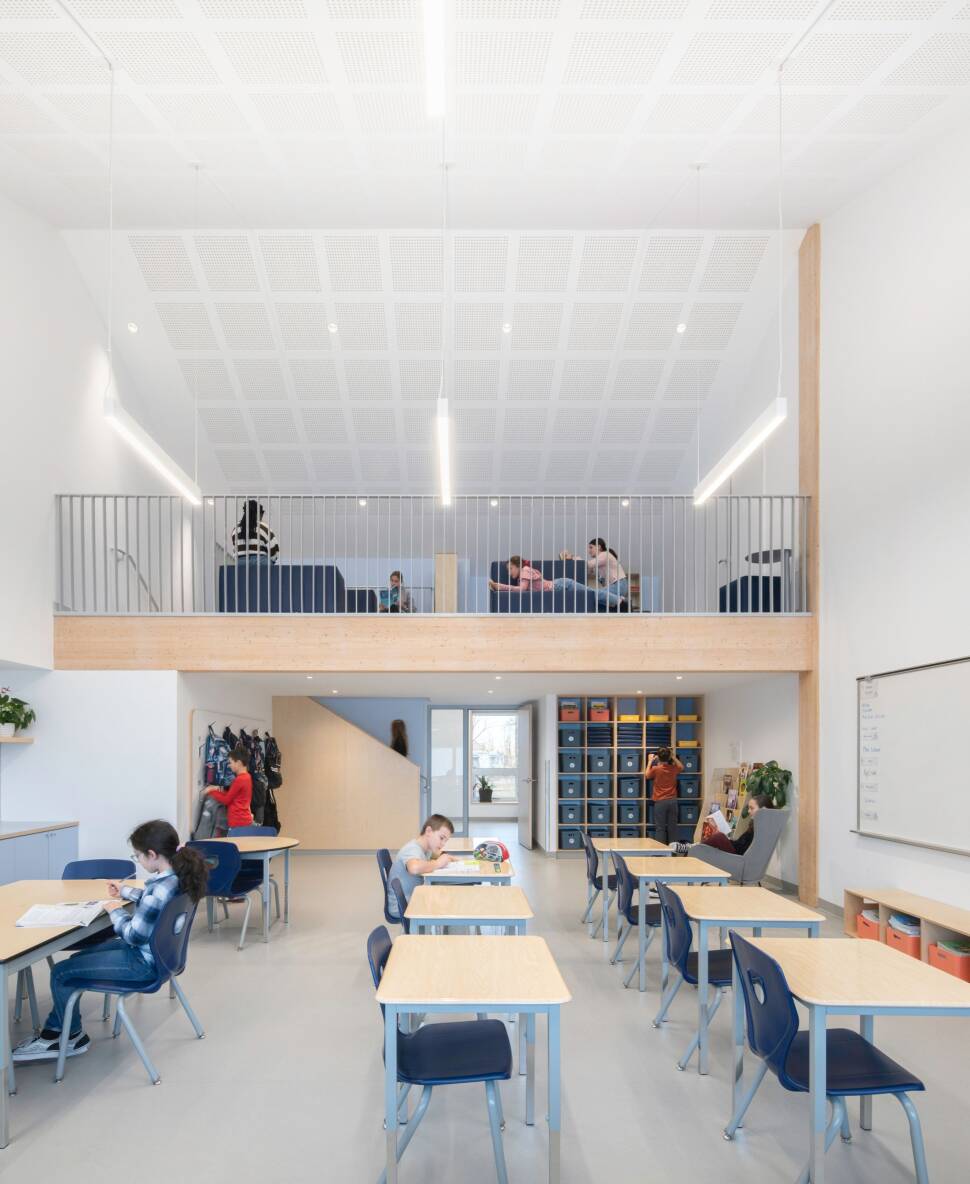
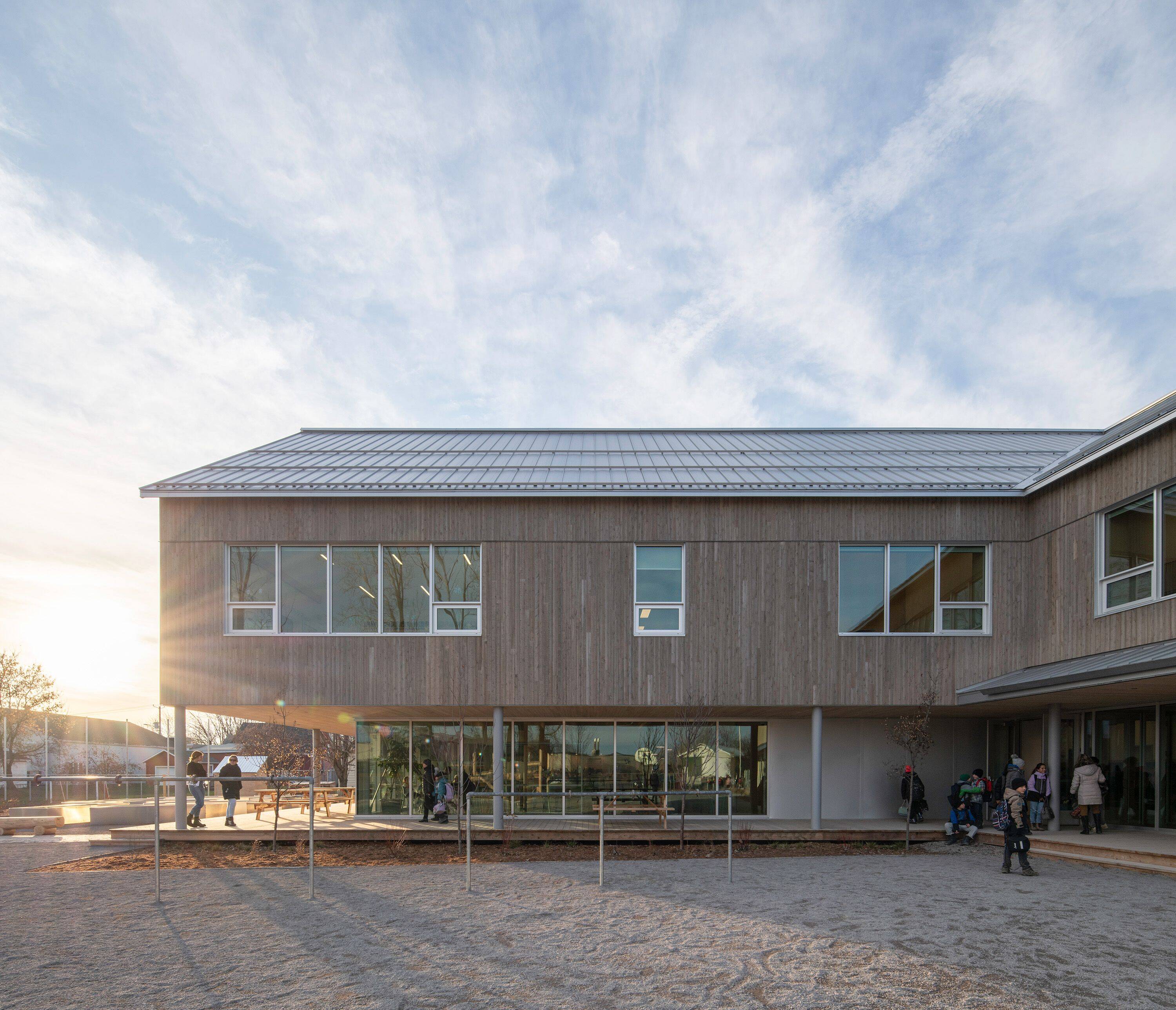
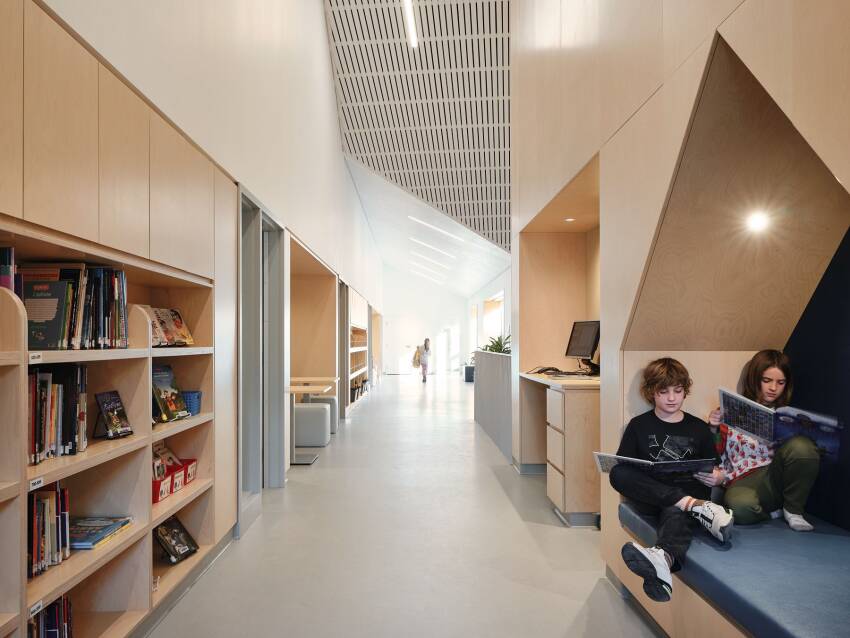
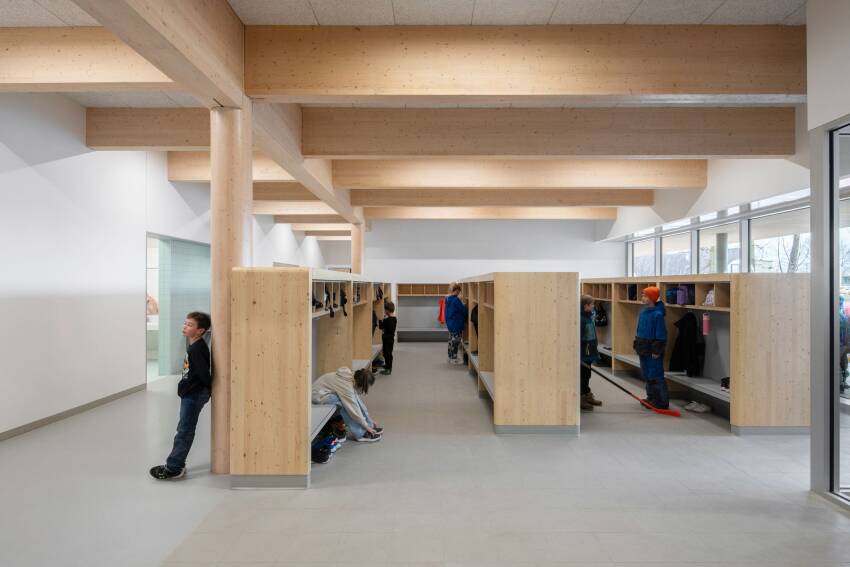
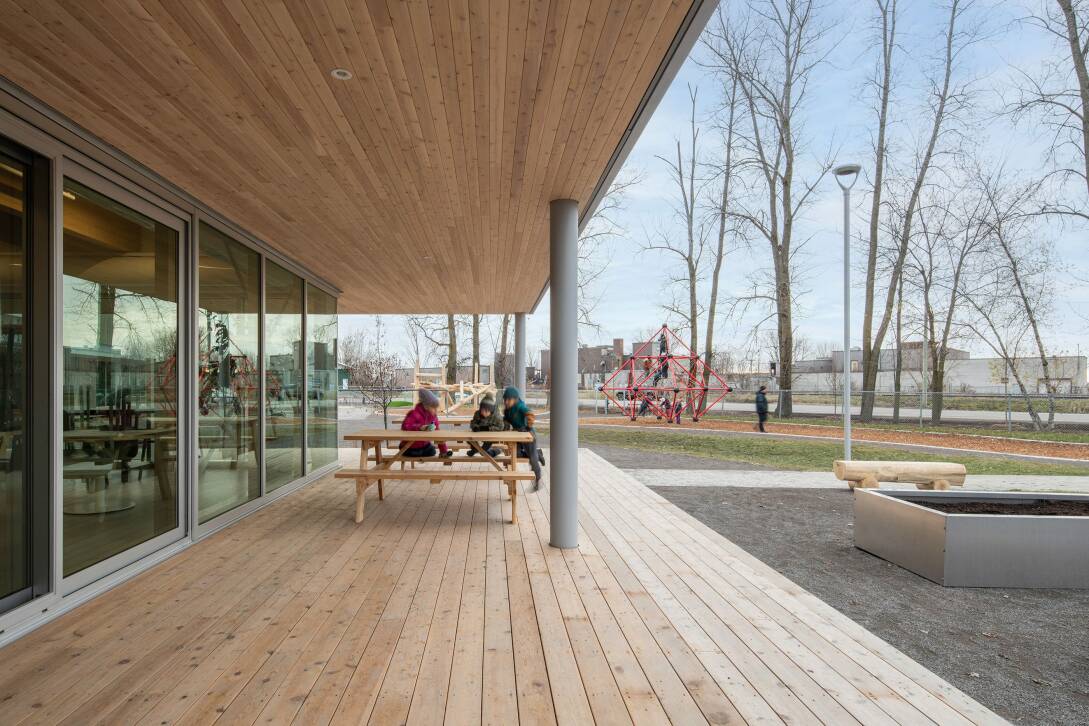
Theoretical analysis of the carbon footprint

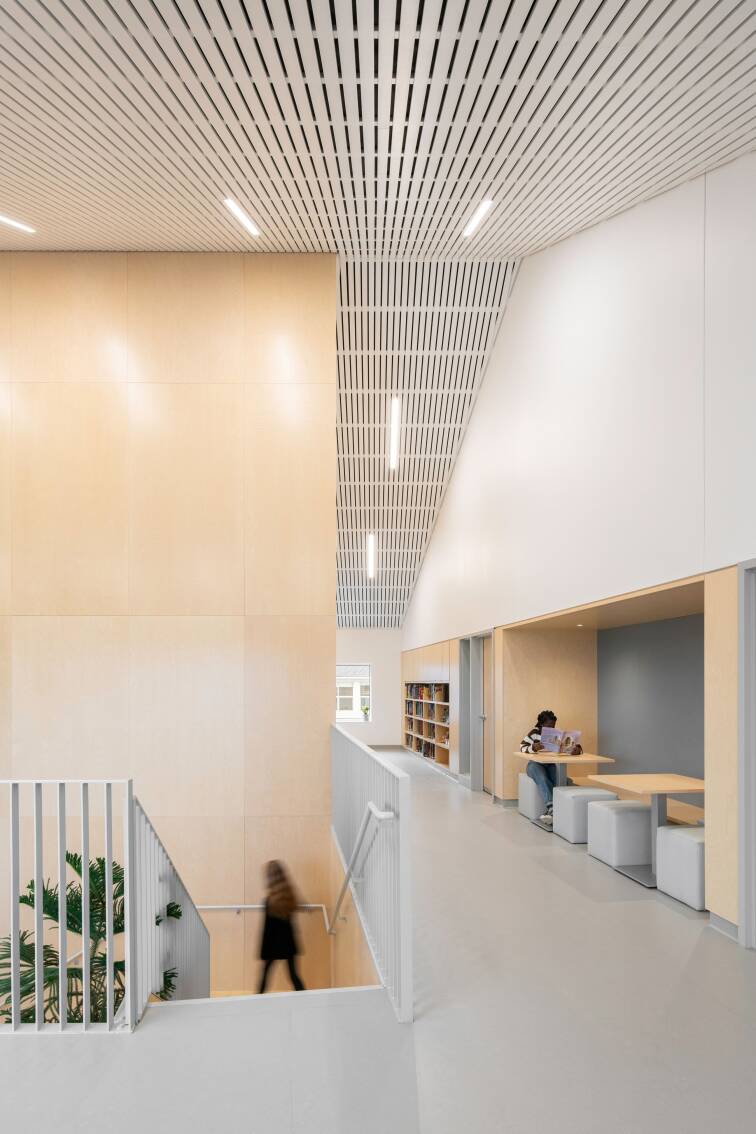
Wood fibre is produced from renewable resources and has a significantly lower carbon footprint than similar alternatives, namely mineral wool in this study. In collaboration with our partners at Cecobois and our team of engineers, at Stantec, we carried out a study using the Gestimat tool, developed by Cecobois. By comparing the bio-based built project with a reference projet designed with a steel structure and mineral wool insulation, we were able to quantify the reduction in greenhouse gas (GHG) emissions linked to the manufacturing of the materials.
In addition to the mass timber structure, the comparative study on Gestimat included the wall and partition framing, and the insulation in the exterior walls. We excluded quantifying non-discriminant elements between the constructed project and the reference project such as foundations, the existing school and all exterior and interior surface finishes.
The manufacturing of the project materials generates approximately an equivalent of 137,345 kg of CO2 or 76 kg of CO2/m². In comparison, the manufacturing of the reference project generates an equivalent of 397,679 kg of CO2 or 220 kg of C02/m². Thus, the built project resulted in a significant reduction in GHG emissions, with a decrease by 260,334 kg CO2 or a reduction by 144 kg CO2/m².
On-site testing
With the goal of measuring in real-time the performance of the envelop, a thermography and a smoke test were conducted to identify and categorize air leakage in the building. Following the infrared thermography, shortcomings were detected in the building envelope and highlighted to the building contractor. The report revealed weaknesses in the performance of the air barrier, localized primarily around the perimeter of doors and curtain walls. These observations show that the infiltrations do not result from poor installation of the membranes or insulation, but rather from the installation of the doors and curtain walls themselves.
Additional work was carried out (sealing, junctions, repairing door thresholds, etc.) to address most of the issues recorded and improve the general performance of the building envelope. However, some issues recorded during this thermography remained unchanged due to the progress of the work site: the shortcomings recorded were not judged to be sufficiently serious to warrant intrusive corrective work in the building envelope, which risked harming its overall performance.
To validate the shortcomings in the building envelope identified during the thermography and confirm the airtightness performance, our team visited the school a second time in the spring of 2025 to conduct smoke tests in the areas where heat loss had been observed.
The final phase of the building envelope assessment involves monitoring the performance of the building enveloppe over a period of two years. Monitoring equipment, installed in strategic places in the building, will enable us to track the critical data of the envelope in real-time (humidity and temperature sensors).
Beginning on-site installation
Results
As soon as the exterior framing was assembled on site, we organized a site inspection together with the building envelope consultant and a representative of the insulation supplier to ensure that the installation of the components was in general conformance with the manufacturer’s recommendations.
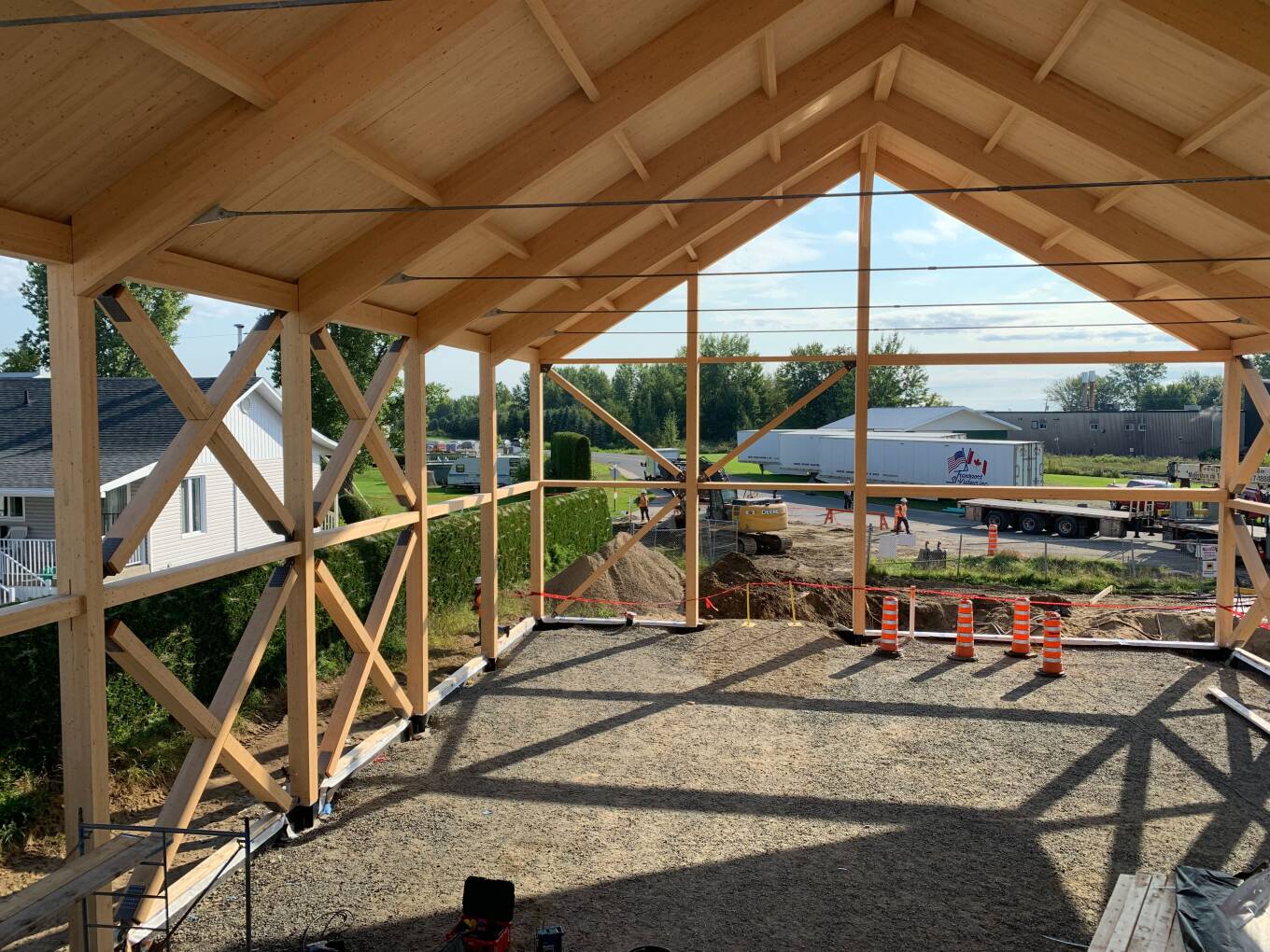
From details to the construction site
In response to climate challenges and energy efficiency requirements, we must acknowledge the urgent need for the construction industry to transition to bio-based materials as a solution to reduce our collective carbon footprint. Among these solutions, wood fibre insulation stands out given its interesting technical properties, particularly its thermal performance, humidity control and low carbon footprint. However, integrating wood fibre insulation in the Canadian context remains a challenge requiring regulatory changes and technical adaptations.
The new addition to the École des Cerisiers, which constitutes a mass-timber project of 2384 m2, demonstrates the potential of wood fibre insulation in the building envelope. This project combines innovation and sustainability by integrating bio-based materials in both the structure and in the building envelope.
Step 1: studying the performance and technical properties of the components of the building envelope
Using wood fibre insulation is not an innovative practice per se, as insulation is manufactured from offcuts from the timber industry. However, using wood fibre insulation in a project of this scale in Canada is innovative.
Two processes are used to manufacture wood fibre insulation: wet and dry. In the wet process, fibres are mixed with water and sometimes with a binder, the mix is mechanically compressed and dried. In the dry process, fibres are sprayed with paraffin, then dried using warm air and applied polyurethane resin. Some dry processes also require hardening of the binder through exposure to a mixture of air and water vapour.
Based on our research, it appears to us that insulation panels manufactured using a dry process are more suitable. In addition, the available range of thickness of panels manufactured using a dry process allows us to achieve our thermal performance targets without laminating several panel thicknesses. Despite the existence of many manufacturers of bio-based insulation products in Québec, none of them currently uses a dry process for insulation.
Managing humidity and dew point
Using wood-based and bio-based insulation in the building envelope requires extreme caution in managing water vapour and condensation: temperature differences in Québec may move the location of dew point according to the season. The location of the vapour barrier may consequently be effective only for part of the year, but encourage condensation within the insulation in the other part of the year. Migration, retention or dew point in a bio-based component may lead to fungal growth or loss of component performance.
To achieve effective airtightness and reduce condensation risks in the assembly of the building envelope, it was necessary to develop assembly involving two membranes, a weather barrier to protect wood components against wind and external water sources, and a vapour barrier to protect against humidity from inside the building. Given the timber frame and mass timber roof frame, the assembly of the building envelope needs air, vapour, and thermal control layers which are permeable to vapour diffusion to prevent putrefaction. This is all the more important when the wall cavities are filled with mattress insulation.
Some insulation, such as mineral wool, glass fibre and wood fibre, allow such vapour diffusion, unlike plastic foams and polystyrene. Multitherm panels and Gutex Thermoflex mattress insulation have similar permeability to rockwool products. However, it is difficult to compare data since Gutex products have not yet been tested under the ASTM E96 standard on “Standard Test Methods for Water Vapour Transmission of Materials”.
Intelligent membranes, such as Pro Clima Intello X vapour barrier, adjust permeability based on changes in humidity. In winter, they become more resistant to diffusion to limit humidity penetrating indoors, while in summer, they promote humidity evacuation towards the building interior, thus ensuring effective drying. Pro Clima Solitex Mento 1000 weather barrier membrane has high vapour permeability allowing humidity in the assembly to evacuate towards the exterior.
Fire resistance of wood fibre insulation
One of the major challenges was the issue of standards and certifications. At present, the majority of wood fibre products are manufactured in Europe and are not fully certified in compliance with North American standards and testing methods.
No wood fibre insulation currently on the market seems to successfully pass the CAN/ULC S114 non-combustibility tests. However, the Gutex Multitherm panel was tested for the flame spread index and smoke developed index in compliance with ASTM E84 and CAN/ULC-S-102. For the ASTM E84 standard, the panel was classified as class B with a flame spread index (FSI) of 65 and smoke developed index (SDI).
No non-combustibility testing or testing for the flame spread index and smoke developed index in compliance with North American standards appears to have been carried out on Gutex Thermoflex mattress insulation. This means that using such insulation in non-combustible walls or fire resistant walls may be compromised as the makeup of building faces must comply with Table 3.2.3.7 “Minimum Construction Requirements for Exposing Building Faces”.
Des Cerisiers primary school is situated in the centre of municipality of Maskinongé, where it serves a community characterized by its agricultural background, the solidarity of its 2300 inhabitants, and its strong community engagement. The project revitalizes the existing school, enabling it to host all the town’s students under the same roof. This project is the only extension project resulting from the province-wide Lab-École design competition. In this unique initiative, and in close collaboration with the local school team, the program was designed to accurately reflect the specific needs and values of the region.
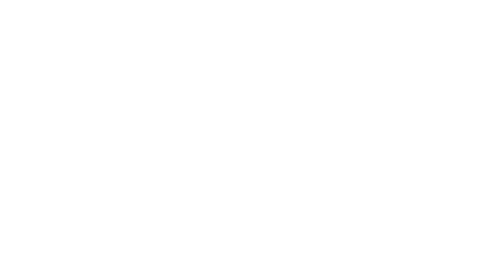
FEATURE
Integrating wood fibre insulation at École des Cerisiers: a case study
By Elaine Tat and Thomas Gauvin-Brodeur
Photographer: David Boyer
Photographer: David Boyer
Photographer: David Boyer
Photographer: David Boyer
Photographer: Taillefer + Paquet + Leclerc Architectes consortium
Photographer: Taillefer + Paquet + Leclerc Architectes consortium
Photographer: Taillefer + Paquet + Leclerc Architectes consortium
Photographer: Taillefer + Paquet + Leclerc Architectes consortium
Photographer: David Boyer
Wood fibre is produced from renewable resources and has a significantly lower carbon footprint than similar alternatives, namely mineral wool in this study. In collaboration with our partners at Cecobois and our team of engineers, at Stantec, we carried out a study using the Gestimat tool, developed by Cecobois. By comparing the bio-based built project with a reference projet designed with a steel structure and mineral wool insulation, we were able to quantify the reduction in greenhouse gas (GHG) emissions linked to the manufacturing of the materials.
In addition to the mass timber structure, the comparative study on Gestimat included the wall and partition framing, and the insulation in the exterior walls. We excluded quantifying non-discriminant elements between the constructed project and the reference project such as foundations, the existing school and all exterior and interior surface finishes.
The manufacturing of the project materials generates approximately an equivalent of 137,345 kg of CO2 or 76 kg of CO2/m². In comparison, the manufacturing of the reference project generates an equivalent of 397,679 kg of CO2 or 220 kg of C02/m². Thus, the built project resulted in a significant reduction in GHG emissions, with a decrease by 260,334 kg CO2 or a reduction by 144 kg CO2/m².
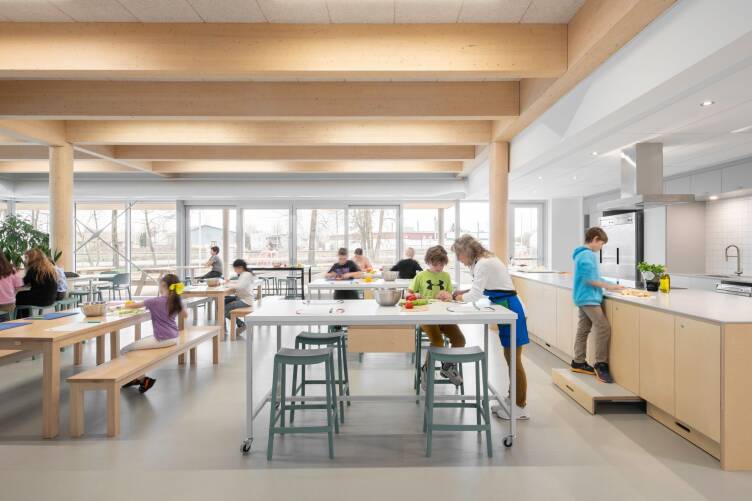
An innovative project at the heart of an engaged community
In 2015, the Government of Québec adopted a policy on integrating wood in construction to encourage the industry to increase the use of wood in public buildings, promote sustainable development, support the local economy and reduce the construction sector’s carbon footprint.
As architects and designers, we have an opportunity to contribute to these objectives by advocating for the integration of wood-based materials in building envelope assemblies as well as in exterior or interior finishes. The use of wood fibre insulation has so far prompted interest from several stakeholders, as well as members from the industry at large, who were excited and willing to collaborate on its integration to a public project.
This project benefited from additional financial support in the form of a subsidy from the Ministère des Ressources naturelles et des Forêts (MRNF) and the backing of the municipality of Maskinongé, which demonstrates a concrete commitment to increasing the integration of wood in construction.
Why would an institutional client take the risk of using wood fibre insulation in the building envelope?
Theoretical analysis of the carbon footprint
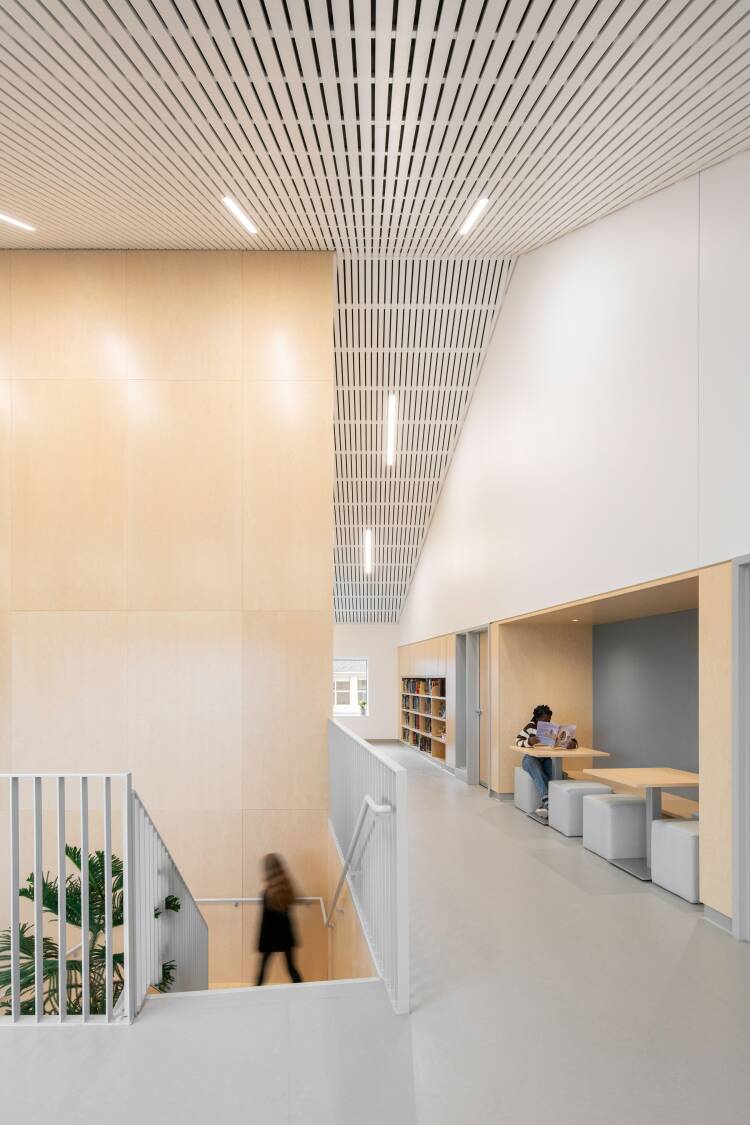
Challenges in the context of publicly funded projects
How to ensure compliance with the procurement rules laid down by the Secrétariat du Conseil du Trésor (Québec) for a public project?
Given that the use of wood fibre insulation is relatively unknown amongst the project team, it was essential for us and our stakeholders to find a way to document and collect real-time data of the envelope’s performance after construction. To deepen the scope and improve the accuracy of this analysis, we decided to collaborate with a building envelope consultant, Envelop3. They assisted us with documenting the performance of the built envelope via a series of on-site tests. These tests allowed us to measure the impact of the wood fibre insulation on the building’s energy efficiency.
How to document the use of wood fibre insulation and its impact on the performance of the building envelope?
As soon as the exterior framing was assembled on site, we organized a site inspection together with the building envelope consultant and a representative of the insulation supplier to ensure that the installation of the components was in general conformance with the manufacturer’s recommendations.
Beginning on-site installation
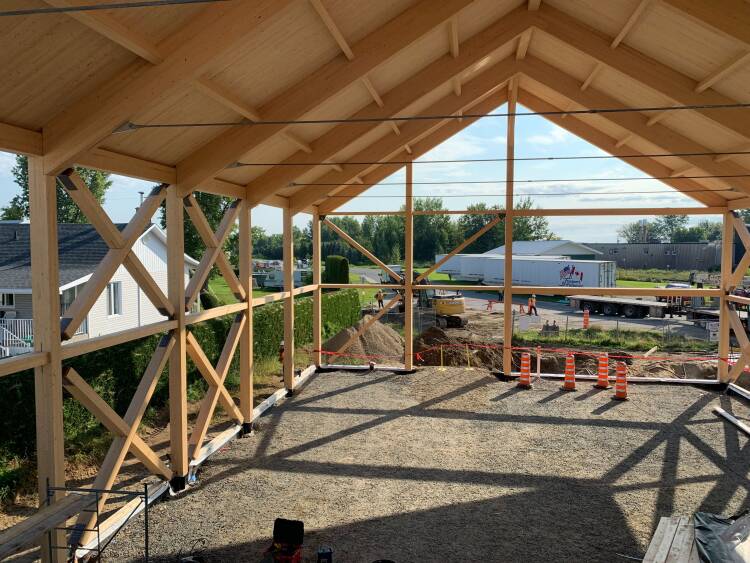
Results
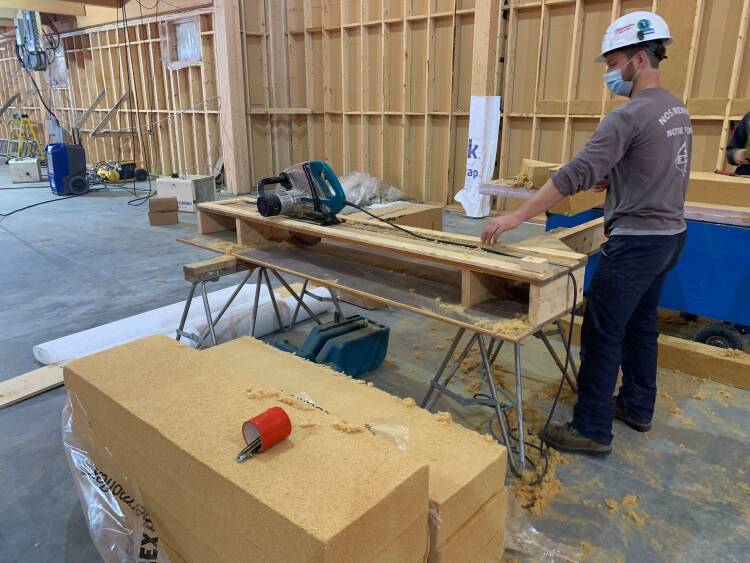
The integration of wood fibre insulation into the building envelope was carried out in three steps: (1) theoretical assessment of the performance and technical properties of the assembly components, (2) comparative analysis against a traditional synthetic and non-bio-based assembly and (3) the development of the building envelope details.
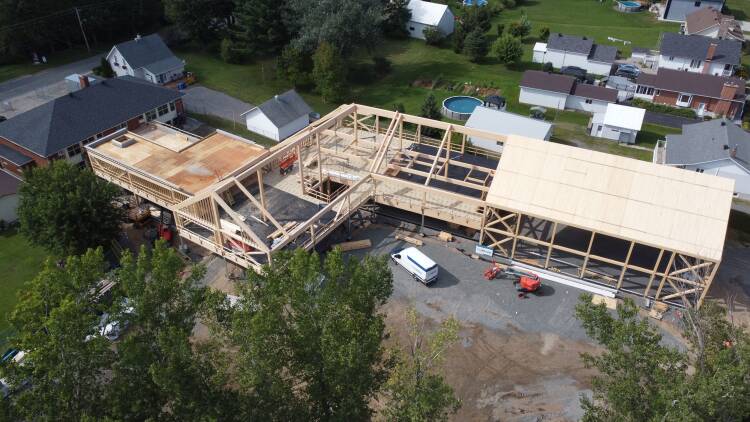
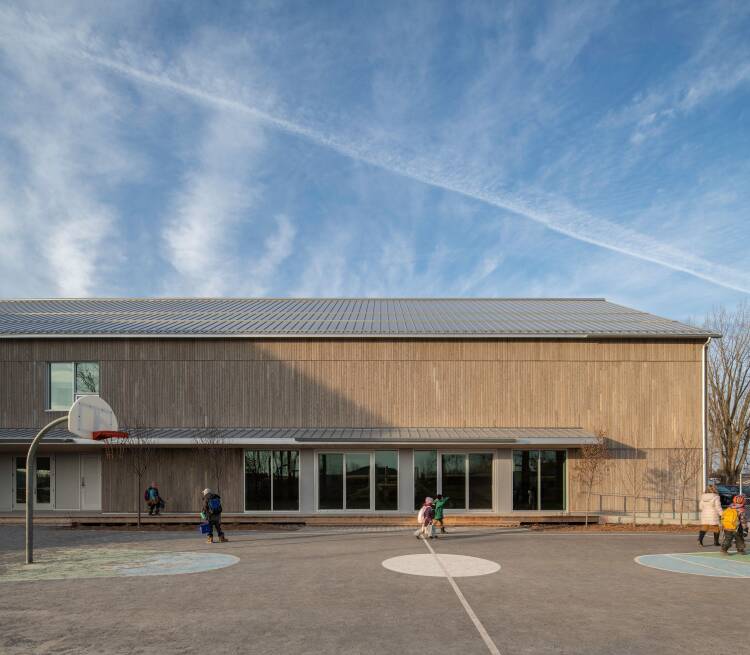
Prospects for the construction industry
The results of on-site testing will allow us to expand and contribute to the database on the performance of wood fibre insulation in building the envelope, specifically adapted to the Québec climate.
In addition to the report on quantifying GHG emissions of construction materials, the project highlights low-carbon options for building assemblies without compromising their energy efficiency. These alternatives to synthetic and non-bio-based materials offer considerable potential for the transition to more sustainable and resilient buildings.
This project forms part of a wider approach aimed at promoting and developing the bio-based insulation industry in Québec and Canada. The wood fibre insulation used in this project had to be imported from Europe, given the lack of equivalencies on the Canadian and Québec markets. This situation highlights the importance of diversifying and reinforcing a local industry, in particular by upcycling waste from the wood processing industry. By encouraging the development and manufacturing of bio-based insulation in Québec, it will be possible to respond to a rapidly growing demand, reduce reliance on imported materials and promote a circular and local economy.
Ultimately, this new school addition embodies a project where innovation and sustainability are core values. Bio-based products are just as seamless to integrate and perform just as effectively as the synthetic systems widely used in the industry. It’s a powerful reminder that even in public institutional projects, sustainability and innovation can go hand in hand.
Architects: Leclerc architectes + Lucie Paquet + Paulette Taillefer
Engineering: Stantec
Landscape architect: Mousse Architecture de Paysage
Enveloppe consultant: Envelop3
General contractor: Therrien Entrepreneur Général
Client: Centre de services scolaire du Chemin-du-Roy
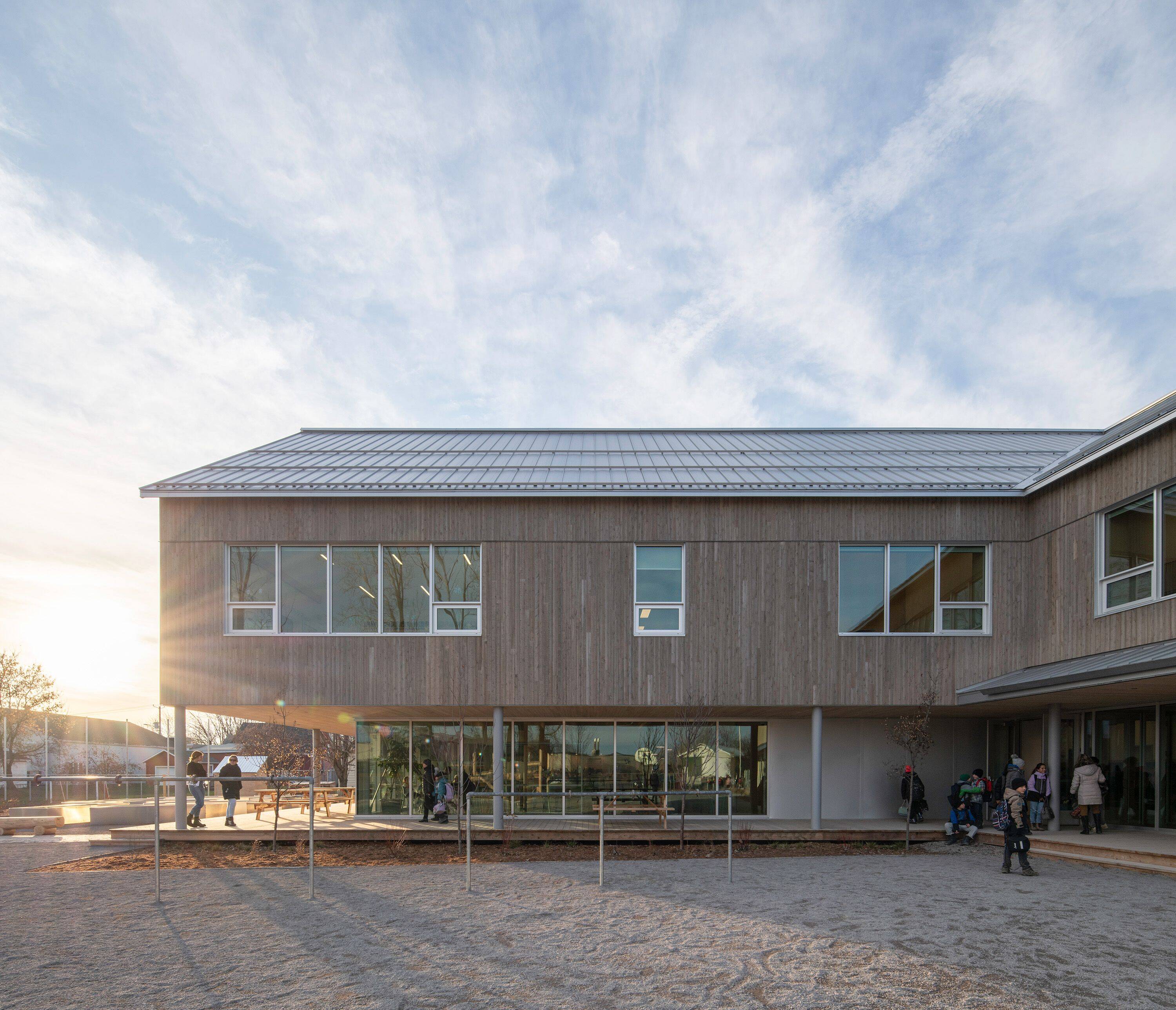
Step 3: working out the critical details of the building envelope
Based on the analysis of the data sheets for the selected products and examples of typical details, we assessed the critical details of the building envelope in collaboration with the consultant specializing in building envelopes.
The typical details covered by the study are:
Junction of the exterior wall with the foundation (sectional view)
Junction of the exterior wall with a window periphery (sectional view and plan view)
Junction of the exterior wall with a curtain wall (sectional view and plan view)
Junction of the exterior wall with the makeup of the roof
Junction of the exterior wall with the soffit and canopy
Details of the ventilated (sloped) roof to reduce thermal bridges
Step 2: comparative analysis with a reference scenario
Wood fibre panels are an interesting alternative to plastic foam insulation or even mineral wool insulation. These rigid panels have similar properties to reference products. The rigidity of these panels also allows a backing panel (in gypsum or plywood) to be removed since an air barrier/weather barrier membrane may be applied directly on them.
In our preliminary analysis, we selected comparable parameters for the reference system (excluding bio-based insulation) and the proposed system (including bio-based insulation). Water vapour permeability, thermal performance, and insulation fitting and installation methods were assessed in each of the systems to ensure a fair comparison.
In our proposed project, we assessed three types of wood fibre insulation to carry out an effective comparison with the reference scenario. In our normal institutional projects, three types of insulation are used in buildings: (1) rigid insulation for the roof, (2) semi-rigid insulation behind the rain screen and (3) mattress insulation between the wood studs in the walls and partitions. In order to extract as much data as possible in this case study, we assessed the equivalents of these three types of wood fibre insulation. However, we did not use rigid insulation for the roof due to budgetary and technical reasons.
The procurement rules around public tenders led us to revise sections of our specification regarding the components of the building envelope. Acceptable products must operate as part of an overall system rather than as individual products, and we ensured compatibility between components through our communications with suppliers. Risks relating to product sourcing, the associated budgetary risks, and technical constraints were also assessed.
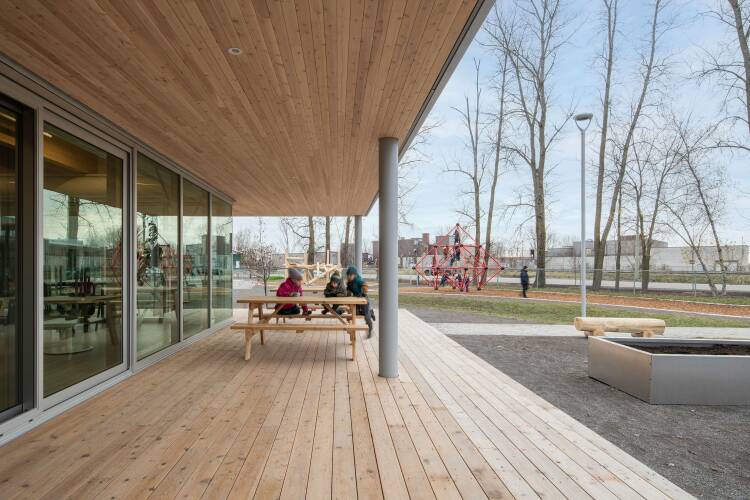
With the goal of measuring in real-time the performance of the envelop, a thermography and a smoke test were conducted to identify and categorize air leakage in the building. Following the infrared thermography, shortcomings were detected in the building envelope and highlighted to the building contractor. The report revealed weaknesses in the performance of the air barrier, localized primarily around the perimeter of doors and curtain walls. These observations show that the infiltrations do not result from poor installation of the membranes or insulation, but rather from the installation of the doors and curtain walls themselves.
Additional work was carried out (sealing, junctions, repairing door thresholds, etc.) to address most of the issues recorded and improve the general performance of the building envelope. However, some issues recorded during this thermography remained unchanged due to the progress of the work site: the shortcomings recorded were not judged to be sufficiently serious to warrant intrusive corrective work in the building envelope, which risked harming its overall performance.
To validate the shortcomings in the building envelope identified during the thermography and confirm the airtightness performance, our team visited the school a second time in the spring of 2025 to conduct smoke tests in the areas where heat loss had been observed.
The final phase of the building envelope assessment involves monitoring the performance of the building enveloppe over a period of two years. Monitoring equipment, installed in strategic places in the building, will enable us to track the critical data of the envelope in real-time (humidity and temperature sensors).
On-site testing
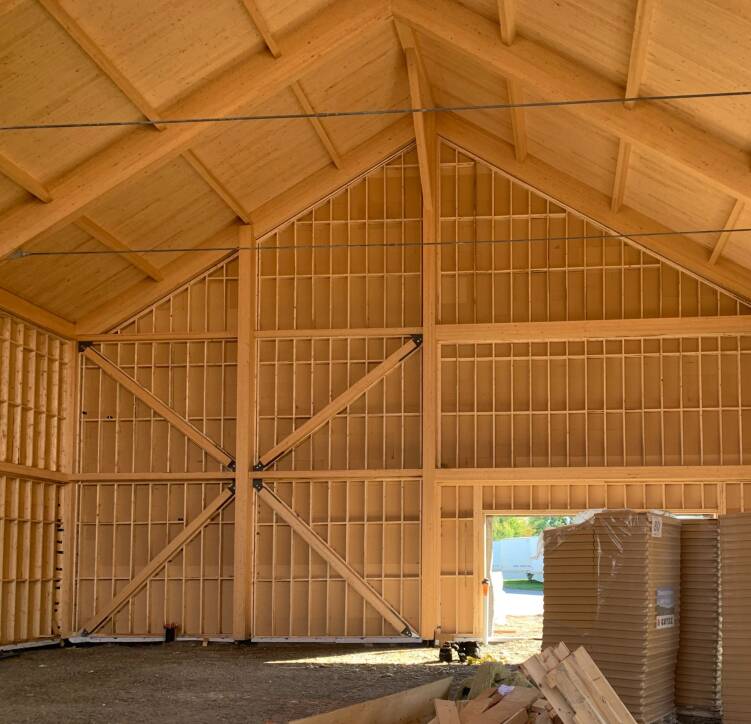
Objectives of this case study
The main objective of this initiative is to assess thermal and environmental performance of wood fibre insulation compared to traditional solutions, while highlighting the challenges linked to integrating wood fibre insulation in Québec construction practices.
In addition, the goal of this project was to show the multiple potential options of integrating wood materials in an educational public building in the interior of the same building, and the resulting benefits (reducing GHG, biophilia, using local manpower, quality learning spaces, etc.).
We hope that École des Cerisiers will be used as an example to highlight the technical performance of this type of insulation, difficulties encountered in the installation stage, solutions adopted and prospects they offer to the construction sector.
Photographer: Maxime Brouillet