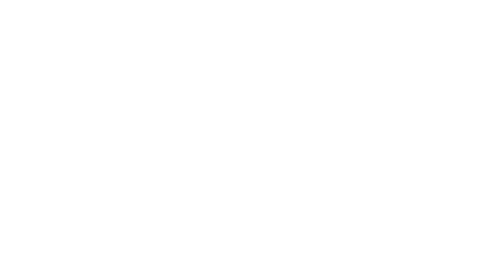
FEATURE
Strength and Resilience
Scroll to Read
At 7:01 AM on 22 August 2023, the former Achillion Restaurant in Prince George, British Columbia, exploded after thieves trying to steal copper ruptured a gas line.
Nine buildings were damaged, including the University of Northern British Columbia's Wood Innovation Research Laboratory (WIRL) located right next door.
The WIRL was already well-known for its design to the International Passive House Standard for energy efficiency and airtightness; Think Wood described it as "a remarkable achievement given the large, exposed surface areas of the building and the region's often cold harsh winters."
However, it is now famous for demonstrating the resilience of well-designed wood buildings, in this case, withstanding the explosion's shock waves, fire and flooding. The glulam frame flexed and returned to normal, having been designed to withstand earthquakes. Debris punctured the wall and spread fire into the interior, but the sprinkler system quickly extinguished it, but flooded the floor.
The most remarkable part of the story is the performance of the exterior wall panels. Many articles discussing the explosion point to the testing of mass timber walls by the US Army in 2016, when they used up to 610 tons of TNT to demonstrate that "mass timber structural systems can effectively resist blast loads in the elastic response range with little noticeable damage." However, the walls of the WIRL were not mass timber; the designers wrote in Canadian Architect:
Passive House designs in cold climates need a lot of insulation, and the walls can get very thick, especially if plastic foam insulation is avoided. It's not uncommon to use inexpensive roof trusses turned on their end to minimize thermal bridging while creating a void that can be filled with insulation.
A local residential truss manufacturer, Winton Global, partially prefabricated the 10-metre high by 2.9-metre wide wall panels, composed of a sheet of Oriented Strand board (OSB), a layer of Intello air and vapour control membrane, and the roof trusses, made from wood sourced from a local sawmill. The panels were craned into place and clipped to the foundations and the glulam frame. The builders then sealed the seams of the membrane and added the exterior OSB sheet, and the void was filled with 500 mm of mineral wool. After adding building wrap and strapping, it was finished with exterior metal cladding.
Marketers for certain competing building materials like to use the catchphrase "build with strength." However, with the WIRL, we have a demonstration of the strength of wood. The exterior wall panels facing the explosion caught fire, and the force of the blast disconnected some of them from the foundations and frame of the building, pushing them in about two inches. But they absorbed the force of the explosion and popped back into place. Dr. Thomas Tannert, Professor in the UNBC School of Engineering, noted in a UNBC video:
The WIRL is a demonstration of the benefits of three different trends in building design and engineering:
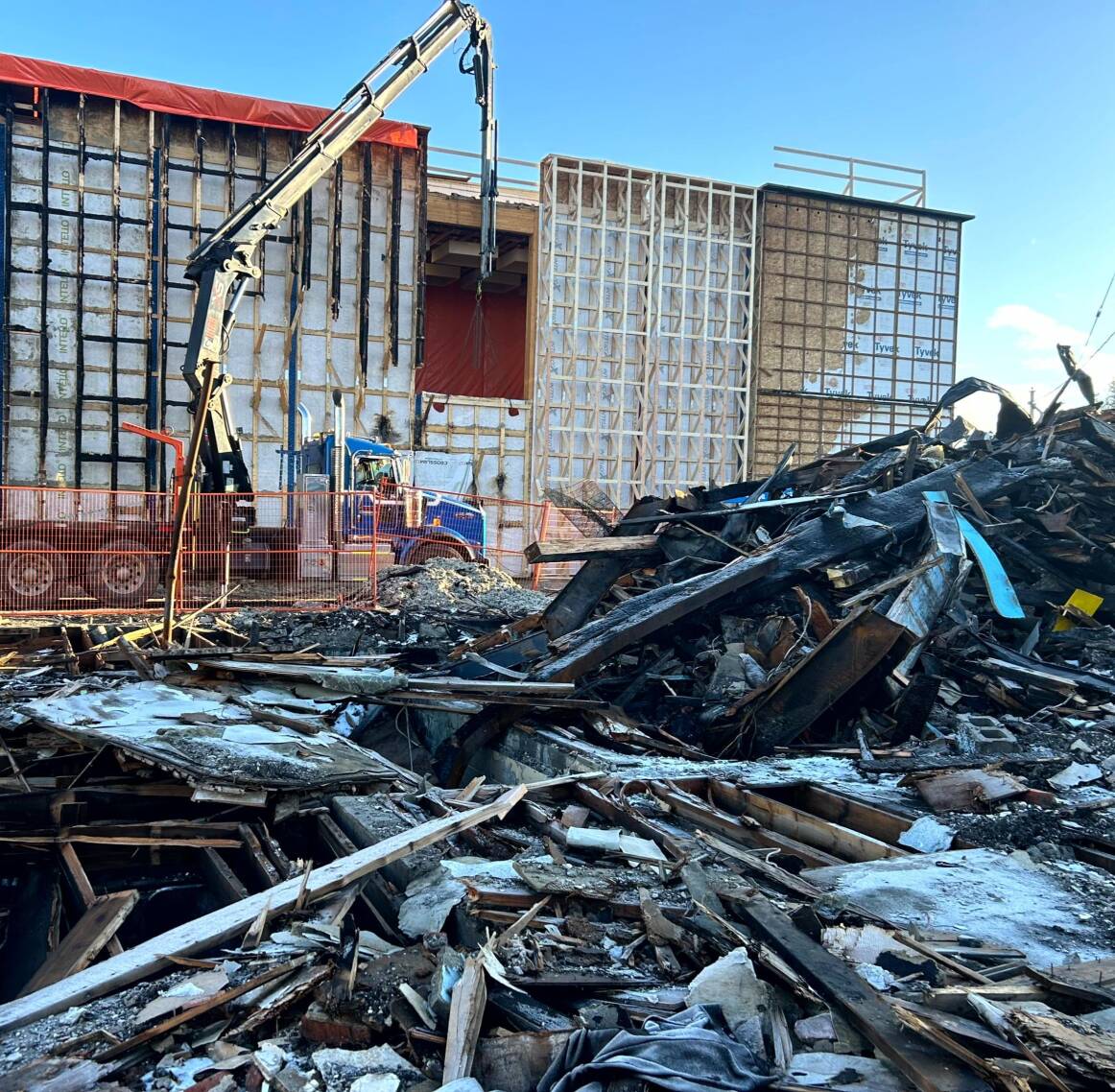
Initially, our team considered using mass-timber wall and roof assemblies with outboard insulation, but found that this approach was not cost-effective. A more feasible solution was achieved with a wall assembly that pairs standard residential roof trusses with sprayed mineral-wool insulation.
Good engineering always goes beyond what the standard requires you to do and current design standards for instance do not require you to consider collapse prevention. However, the building, the way it was designed, actually did withstand a blast right next door without any single element collapsing, so that is really a sign of good engineering.
Prefabrication
After the explosion, the panel manufacturer, a local truss shop, didn't even have to come out and measure for the new panels; they built new ones to the previous specifications and popped right in. There are few prefabricated elements as common as roof trusses or as efficient in their use of wood; turning them on their end is a clever and cost-effective use of the technology.
Using lightweight wood framing made the original construction and the reconstruction after the fire significantly faster.
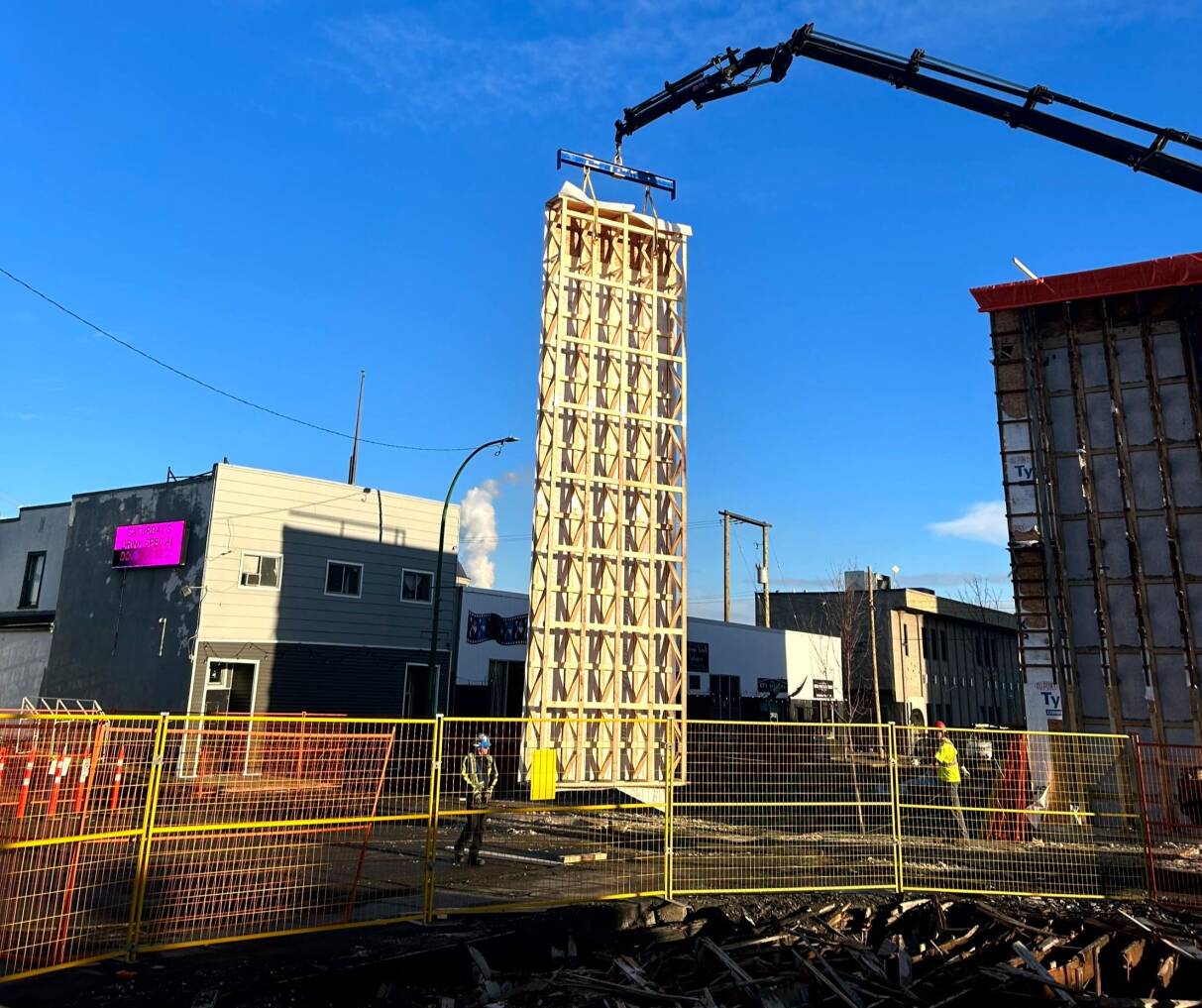
Passive House
WIRL was the first industrial building in North America to be certified to the Passive House Standard and uses 90% less energy for heating and cooling than comparable buildings. They are known for their thermal resilience.
But this explosion raises the question: did meeting the Passive House Standard increase its structural resilience? Did having 500 mm of insulation help absorb the shock of the blast?
Stantec architect Derreck Travis responded in an email:
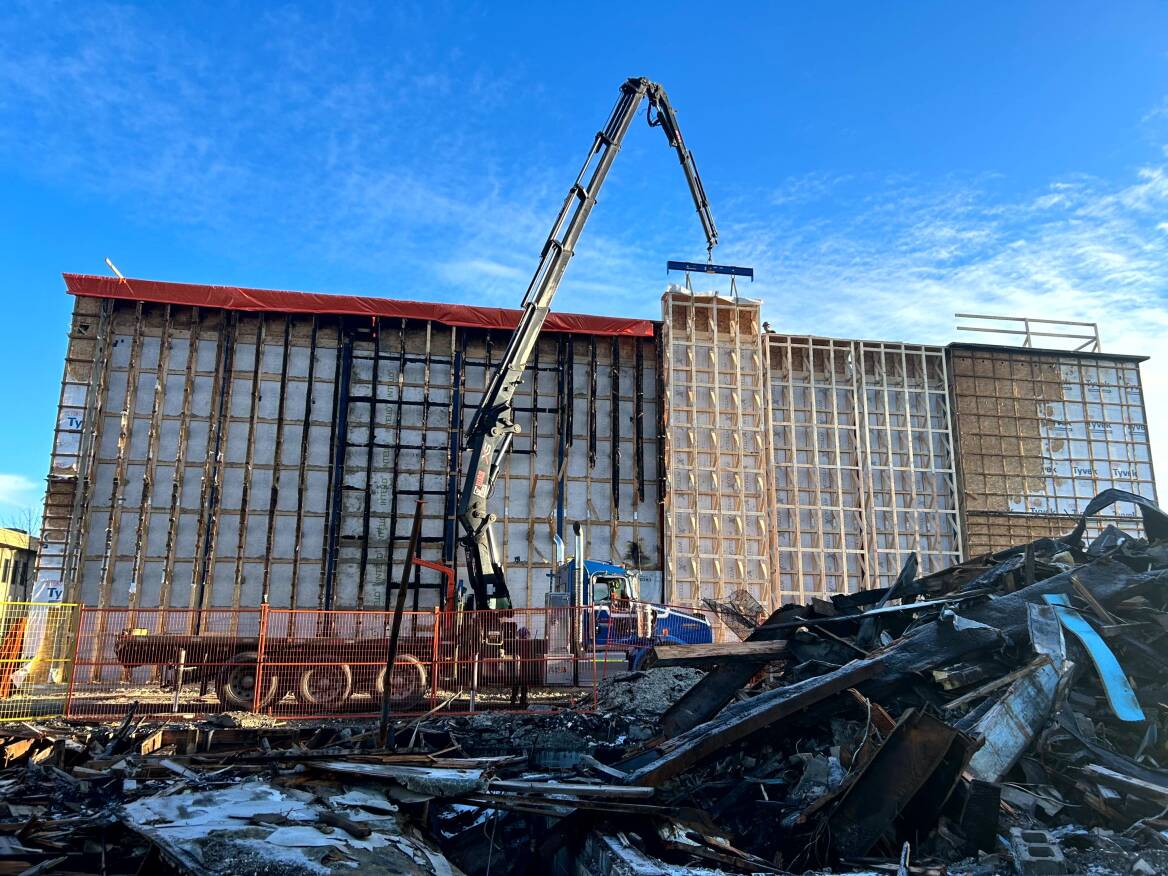
A lot of what we know about the damage resulting from the explosion is speculation, but the construction assemblies played a significant part in its resilience. The non-combustible mineral wool insulation encapsulated the wood truss members and acted to protect them during the fire. The I am unsure the insulation absorbed the shock but the wood trusses are designed for significant loading and were able to withstand the load of the explosion.
Wood Construction
It is almost Karma that the explosion happened next door to a building designed as a wood innovation research lab; what better way to demonstrate the strength and resilience of the material?
In the end, the sprinkler system caused most of the damage. David Claus, UNBC's director of facilities, noted:
The sprinkler came on and put out the fire like it's supposed to, and there was a bit of charring on a couple of pieces of wood. But the water (which ran for more than a full day) got some equipment wet, and unfortunately, some of the most expensive equipment was right where the fire came through.
One of the main reasons for building with wood is to reduce lifecycle carbon emissions; the WIRL, with its wood construction and Passive House standard, knocks full life cycle carbon emissions down by 70%.
Historically, the main reason for not building with wood was the fear of fire; the WIRL demonstrates that even in the face of a massive explosion a few meters away, wood construction is strong, resilient, capable of bending and not breaking.
This may be the best bit of research to come out of the Wood Innovation Research Laboratory. As Derreck Travis notes:
The biggest lesson that I can see is the benefits of resiliency. In a climate where construction is expensive, the construction of the WIRL allowed the building to withstand the explosion with minimal damage and the areas that were damaged were able to be replaced relatively easily due to the modularity of the wall panels.
The WIRL is a demonstration of the benefits of three different trends in building design and engineering:
It is almost Karma that the explosion happened next door to a building designed as a wood innovation research lab; what better way to demonstrate the strength and resilience of the material?
In the end, the sprinkler system caused most of the damage. David Claus, UNBC's director of facilities, noted:
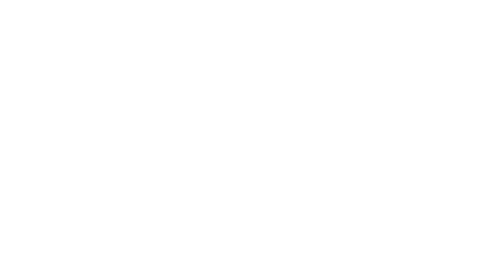
FEATURE
Strength and Resilience
The sprinkler came on and put out the fire like it's supposed to, and there was a bit of charring on a couple of pieces of wood. But the water (which ran for more than a full day) got some equipment wet, and unfortunately, some of the most expensive equipment was right where the fire came through.
At 7:01 AM on 22 August 2023, the former Achillion Restaurant in Prince George, British Columbia, exploded after thieves trying to steal copper ruptured a gas line.
Nine buildings were damaged, including the University of Northern British Columbia's Wood Innovation Research Laboratory (WIRL) located right next door.
The WIRL was already well-known for its design to the International Passive House Standard for energy efficiency and airtightness; Think Wood described it as "a remarkable achievement given the large, exposed surface areas of the building and the region's often cold harsh winters."
However, it is now famous for demonstrating the resilience of well-designed wood buildings, in this case, withstanding the explosion's shock waves, fire and flooding. The glulam frame flexed and returned to normal, having been designed to withstand earthquakes. Debris punctured the wall and spread fire into the interior, but the sprinkler system quickly extinguished it, but flooded the floor.
The most remarkable part of the story is the performance of the exterior wall panels. Many articles discussing the explosion point to the testing of mass timber walls by the US Army in 2016, when they used up to 610 tons of TNT to demonstrate that "mass timber structural systems can effectively resist blast loads in the elastic response range with little noticeable damage." However, the walls of the WIRL were not mass timber; the designers wrote in Canadian Architect:
Passive House designs in cold climates need a lot of insulation, and the walls can get very thick, especially if plastic foam insulation is avoided. It's not uncommon to use inexpensive roof trusses turned on their end to minimize thermal bridging while creating a void that can be filled with insulation.
A local residential truss manufacturer, Winton Global, partially prefabricated the 10-metre high by 2.9-metre wide wall panels, composed of a sheet of Oriented Strand board (OSB), a layer of Intello air and vapour control membrane, and the roof trusses, made from wood sourced from a local sawmill. The panels were craned into place and clipped to the foundations and the glulam frame. The builders then sealed the seams of the membrane and added the exterior OSB sheet, and the void was filled with 500 mm of mineral wool. After adding building wrap and strapping, it was finished with exterior metal cladding.
Marketers for certain competing building materials like to use the catchphrase "build with strength." However, with the WIRL, we have a demonstration of the strength of wood. The exterior wall panels facing the explosion caught fire, and the force of the blast disconnected some of them from the foundations and frame of the building, pushing them in about two inches. But they absorbed the force of the explosion and popped back into place. Dr. Thomas Tannert, Professor in the UNBC School of Engineering, noted in a UNBC video:
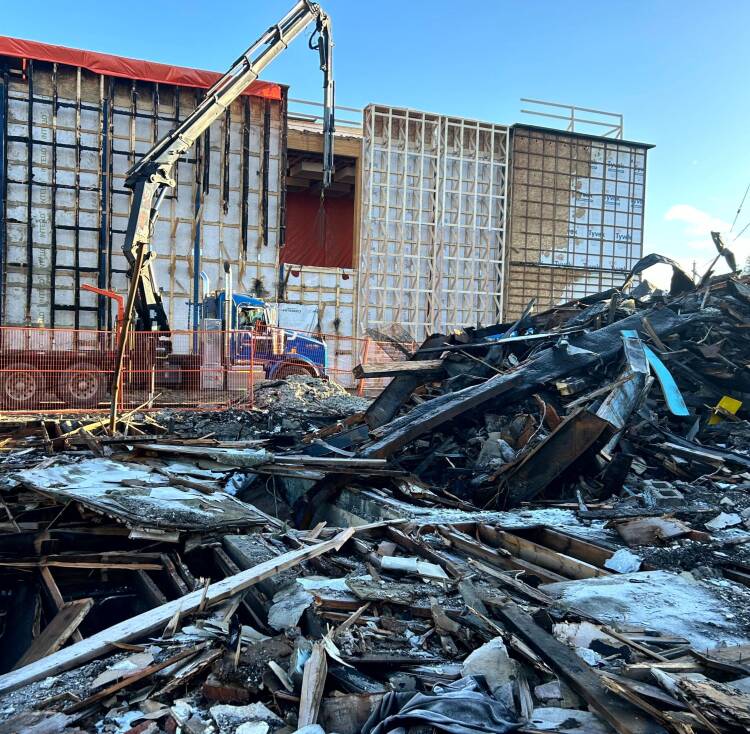
One of the main reasons for building with wood is to reduce lifecycle carbon emissions; the WIRL, with its wood construction and Passive House standard, knocks full life cycle carbon emissions down by 70%.
Historically, the main reason for not building with wood was the fear of fire; the WIRL demonstrates that even in the face of a massive explosion a few meters away, wood construction is strong, resilient, capable of bending and not breaking.
This may be the best bit of research to come out of the Wood Innovation Research Laboratory. As Derreck Travis notes:
The biggest lesson that I can see is the benefits of resiliency. In a climate where construction is expensive, the construction of the WIRL allowed the building to withstand the explosion with minimal damage and the areas that were damaged were able to be replaced relatively easily due to the modularity of the wall panels.
Initially, our team considered using mass-timber wall and roof assemblies with outboard insulation, but found that this approach was not cost-effective. A more feasible solution was achieved with a wall assembly that pairs standard residential roof trusses with sprayed mineral-wool insulation.
Prefabrication
After the explosion, the panel manufacturer, a local truss shop, didn't even have to come out and measure for the new panels; they built new ones to the previous specifications and popped right in. There are few prefabricated elements as common as roof trusses or as efficient in their use of wood; turning them on their end is a clever and cost-effective use of the technology.
Using lightweight wood framing made the original construction and the reconstruction after the fire significantly faster.
In both tests, the fire decayed once the fuel load (wood cribs used to simulate combustible construction materials) was consumed in the fire. In the first test, a garbage can fire was used, which, after a prolonged period, was able to ignite the structure. However, the structure fire lasted roughly two minutes, since the garbage can fire was insufficient to keep the structure involved in fire.
In the second test, a full corner bay of the structure was used with a relatively high fuel load. Similar to the fire scenarios in a completed mass timber building, the fire burned out once the movable fuel load was consumed. In this case, due to the wind, the structure experienced smoldering hot spots at connections and joints between the mass timber components after the fire had burned out, which required fire services to extinguish them.
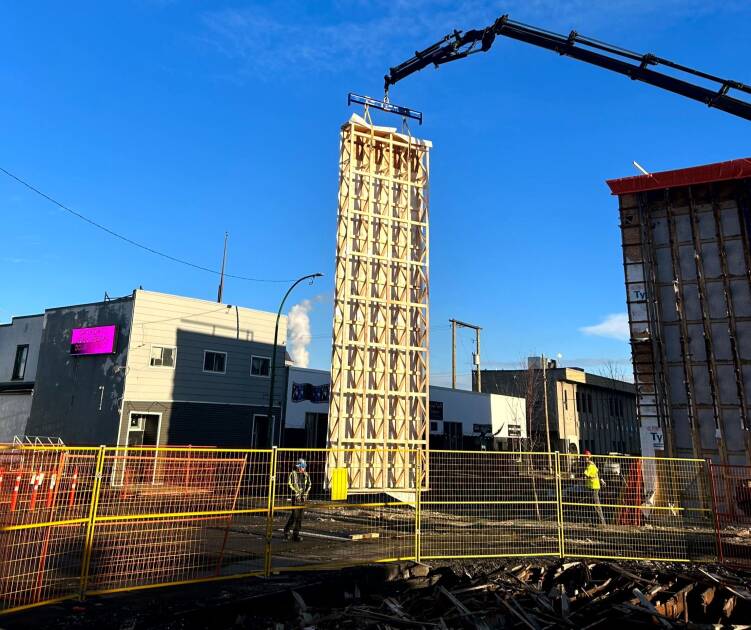
Passive House
WIRL was the first industrial building in North America to be certified to the Passive House Standard and uses 90% less energy for heating and cooling than comparable buildings. They are known for their thermal resilience.
But this explosion raises the question: did meeting the Passive House Standard increase its structural resilience? Did having 500 mm of insulation help absorb the shock of the blast?
Stantec architect Derreck Travis responded in an email:
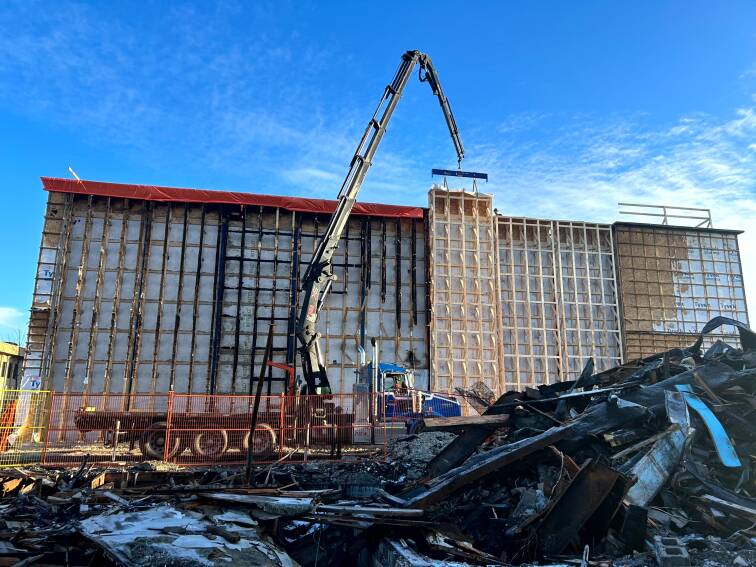
A lot of what we know about the damage resulting from the explosion is speculation, but the construction assemblies played a significant part in its resilience. The non-combustible mineral wool insulation encapsulated the wood truss members and acted to protect them during the fire. The I am unsure the insulation absorbed the shock but the wood trusses are designed for significant loading and were able to withstand the load of the explosion.
Wood Construction
Good engineering always goes beyond what the standard requires you to do and current design standards for instance do not require you to consider collapse prevention. However, the building, the way it was designed, actually did withstand a blast right next door without any single element collapsing, so that is really a sign of good engineering.