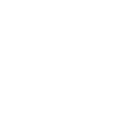
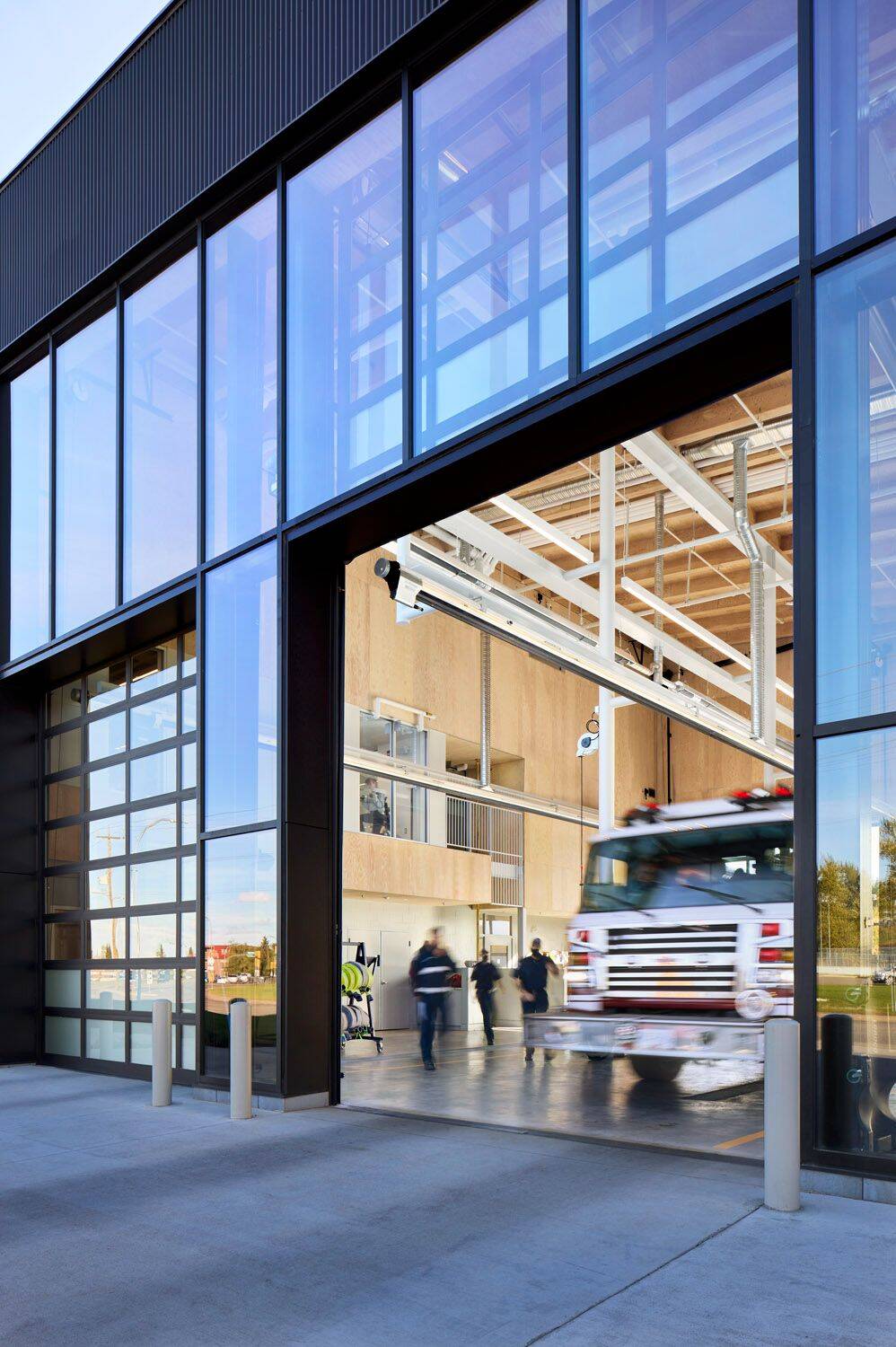
The NLT stairwell at the front entrance was site fabricated with a fully randomized pattern of boards. Crews used more than 100,000 fasteners and more than 3,000 pieces of lumber to construct it. Within the main stair space, the user is completely immersed within the wood volume, with other materials only introduced where absolutely required. To enhance this experience, extensive efforts were taken to ensure that all connections were concealed.LVL and plywood decking were used for the roof of the facility’s large expansive truck bays. Wood was also used throughout the interior as a finishing material. The overall use of wood offers visual warmth.But the use of timber demonstrates more than just visual warmth. Wood is a trusted, fire-safe, and durable material. For example, if NLT or LVL is exposed to flame, the material chars, forming a protective layer.Along with this important aspect, the use of exposed wood also adds biophilic benefits for the fire station’s employees.
A fire station constructed with wood seems counterintuitive, but that wasn’t the case for the station in Prince George, B.C. Wood was the material of choice for the structure—in part to highlight the area’s history with the timber industrysince the early 20th century.
The 2,500 m2 Prince George Fire Hall No. 1—which replaces the former smaller, 60-year-old facility—is actually a hybrid of wood, steel, and concrete. It accommodates five drive-through truck bays, an emergency operations centre, a dispatch, and administrative offices.
Several main elements within the hall were conceptualized as being wood, which was used both as a structural material—and as a means of expression.
The apparatus bays, for example, were conceptualized as a wood-lined volume that would be visible from the adjacent street and park. With a large amount of equipment and a number of fixtures that are needed in these bays, the wood surfaces throughout the space provide a calm, simple backdrop.
The 2,500 m2 Prince George Fire Hall No. 1—which replaces the former smaller, 60-year-old facility—is actually a hybrid of wood, steel, and concrete. It accommodates five drive-through truck bays, an emergency operations centre, a dispatch, and administrative offices.
Several main elements within the hall were conceptualized as being wood, which was used both as a structural material—and as a means of expression.
The apparatus bays, for example, were conceptualized as a wood-lined volume that would be visible from the adjacent street and park. With a large amount of equipment and a number of fixtures that are needed in these bays, the wood surfaces throughout the space provide a calm, simple backdrop.
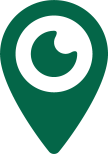
Prince George, B.C.
WOOD CHIPS
WINNING PROJECTS
Prince George Fire Hall No. 1
Prince George Fire Hall No. 1
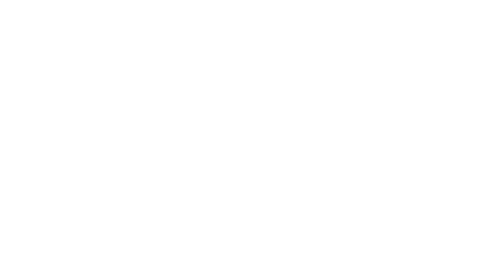
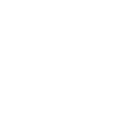
Previous Project
Next Project
Of course, timber, vs concrete and steel, has significantly reduced carbon emissions. In fact, timber stores carbon and is renewable if it’s harvested from sustainable forestry production. HAUT is an example of a sustainable structure in other ways. The building is fitted with solar panels on the roof and façade, cooling is sourced from the ground, and sensor-controlled thermostats adjust low-temperature floor heating and cooling. There are nesting boxes for birds and bats, charging points for shared electric cars, and a rooftop garden with rainwater storage.
The design of HAUT has helped to accelerate the shift from traditional construction in concrete and steel to timber as the more sustainable alternative.
The design of HAUT has helped to accelerate the shift from traditional construction in concrete and steel to timber as the more sustainable alternative.
HAUT, the residential apartment in Amsterdam, serves as a prototype for building innovative and environmentally-friendly high-rise timber structures. This 21-floor timber skyscraper received a BREEAM rating of Outstanding, the highest sustainability rating awarded to a residential building in the Netherlands.The total gross floor area is roughly 14,500 m², within which is a commercial/public plinth, cycle storage space, and underground car park. The residential tower, 73 m high, has 52 apartments of different sizes.The load-bearing structure of HAUT is made of CLT panels manufactured off-site, ensuring low waste production and fast, clean on-site assembly. As there are no standard building regulations for high-rise timber construction, the design team has invested much time and energy in technical innovation and safety. Floors and walls are constructed in timber, but a structure made completely of timber in the wet and windy conditions of the city would be impossible. As a result, the foundations, basement, and core are constructed in concrete.
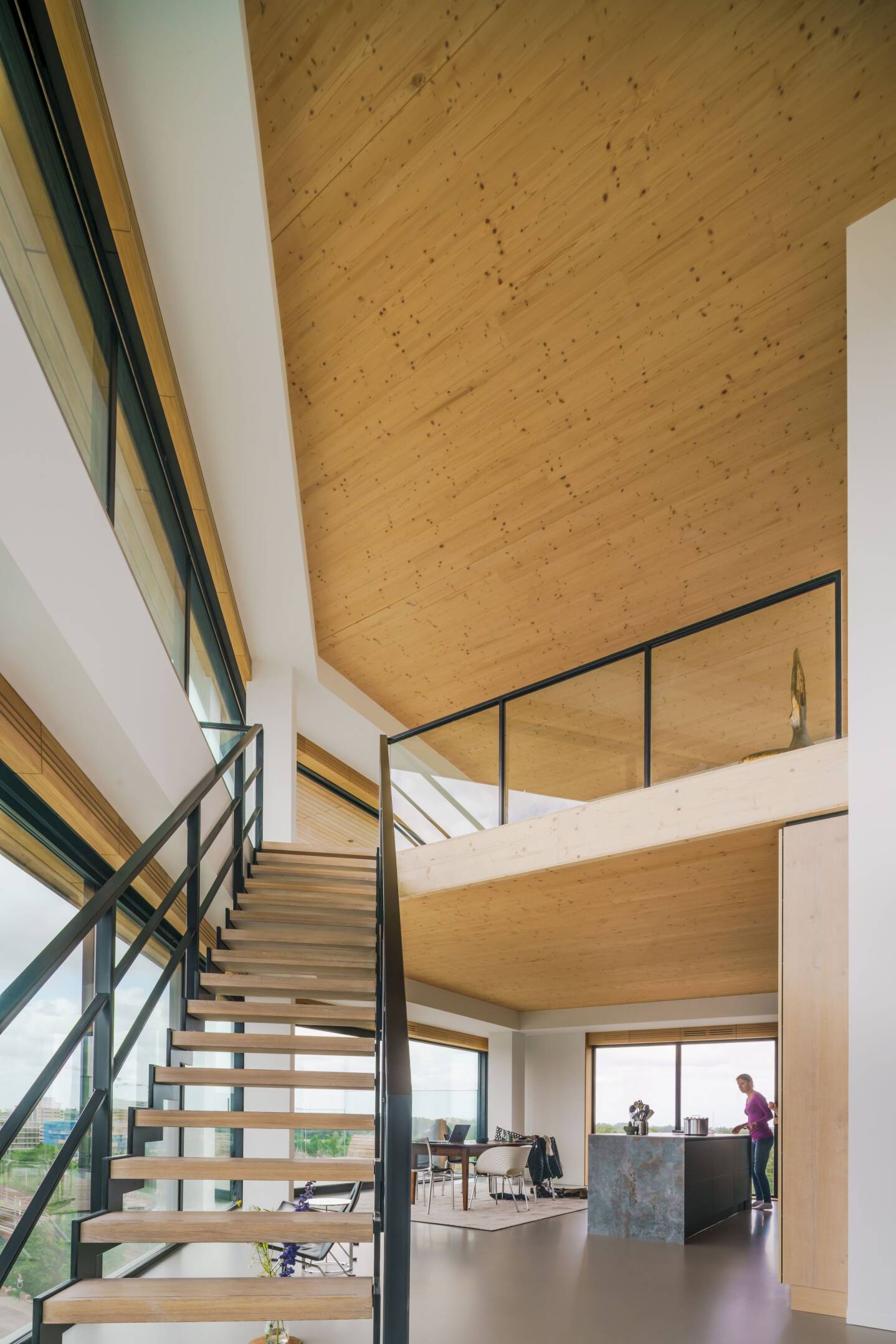
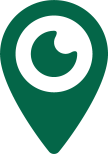
Amsterdam, The Netherlands
WOOD CHIPS
WINNING PROJECTS
HAUT
HAUT
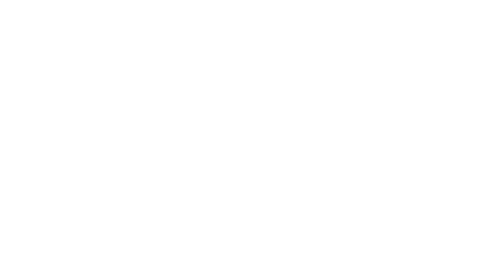
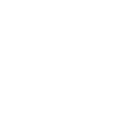
Previous Project
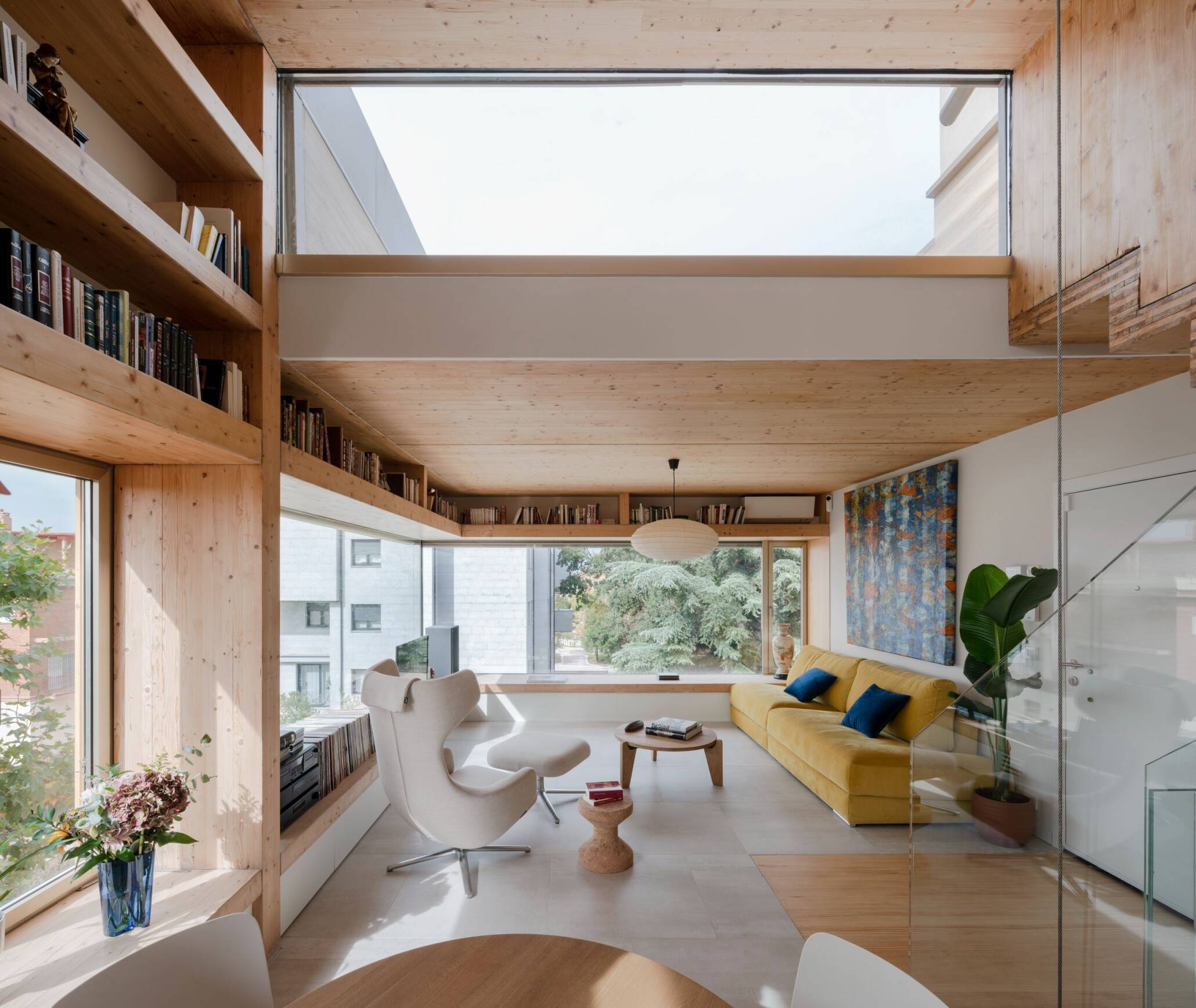
Our-Shelves-Houses in Madrid, Spain, is a co-op building of eight duplex houses that share a common access area and two vertical communication cores. Each of the eight houses has three bedrooms, each room is staggered, and there is elevator service on all floors. The complex also has a swimming pool, garden, and parking.
The co-op building is set back to allow access to Hernández Rubín Street, creating an area for common private use. In the rear area, there is another garden space for common private use.
All of the apartments have a private outdoor space, a garden (for the lower apartments) or a terrace (for the upper ones). In addition, the building offers unique features that allow each co-op member to customize their own home.
The wooden structure allows for sun protection, privacy control, and integrated furniture, among other elements. The staggering of the floors improves communication between rooms and provides for visual connections with terraces and gardens.
The structural system of the five-storey building is composed of CLT panels and laminated wood elements. The CLT panels form the floor slabs and also appear on the façade combined with some glulam beams forming “ribs” for the building envelope. The first floor is formed by a concrete slab, reinforced by its contact with the ground, and steel struts at the corners to solve the overhangs.
The CLT and GLT structure of spruce and pine, and the GL24h class CLT slabs on ceilings, offer sustainability, hygrothermal, and easy assembly advantages.
The use of CLT as a load-bearing material allowed it to be the finishing material, which reduced the project’s labour and execution time.
The building’s installations are resolved by means of an aerothermal system with heat exchange that ensures hygrothermal comfort and ventilation of the apartments with maximum efficiency. In addition, a rainwater collection system is used to use rainwater for irrigation and toilets, and solar thermal panels support the aerothermal machines. Finally, the apartments have mechanical ventilation with heat recovery, ensuring the correct ventilation of each room without the need to open the windows.
The co-op building is set back to allow access to Hernández Rubín Street, creating an area for common private use. In the rear area, there is another garden space for common private use.
All of the apartments have a private outdoor space, a garden (for the lower apartments) or a terrace (for the upper ones). In addition, the building offers unique features that allow each co-op member to customize their own home.
The wooden structure allows for sun protection, privacy control, and integrated furniture, among other elements. The staggering of the floors improves communication between rooms and provides for visual connections with terraces and gardens.
The structural system of the five-storey building is composed of CLT panels and laminated wood elements. The CLT panels form the floor slabs and also appear on the façade combined with some glulam beams forming “ribs” for the building envelope. The first floor is formed by a concrete slab, reinforced by its contact with the ground, and steel struts at the corners to solve the overhangs.
The CLT and GLT structure of spruce and pine, and the GL24h class CLT slabs on ceilings, offer sustainability, hygrothermal, and easy assembly advantages.
The use of CLT as a load-bearing material allowed it to be the finishing material, which reduced the project’s labour and execution time.
The building’s installations are resolved by means of an aerothermal system with heat exchange that ensures hygrothermal comfort and ventilation of the apartments with maximum efficiency. In addition, a rainwater collection system is used to use rainwater for irrigation and toilets, and solar thermal panels support the aerothermal machines. Finally, the apartments have mechanical ventilation with heat recovery, ensuring the correct ventilation of each room without the need to open the windows.
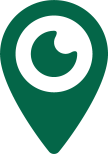
Madrid, Spain
WOOD CHIPS
WINNING PROJECTS
Our-Shelves-Houses
Our-Shelves-Houses
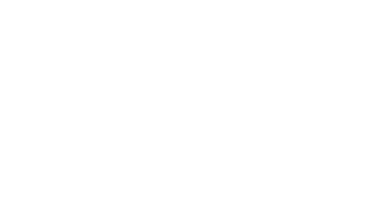
WOOD CHIPS

TheNLT stairwell at the front entrance was site fabricated with a fully randomized pattern of boards. Crews used more than 100,000 fasteners and more than 3,000 pieces of lumber to construct it. Within the main stair space, the user is completely immersed within the wood volume, with other materials only introduced where absolutely required. To enhance this experience, extensive efforts were taken to ensure that all connections were concealed.LVL and plywood decking were used for the roof of the facility’s large expansive truck bays. Wood was also used throughout the interior as a finishing material. The overall use of wood offers visual warmth.But the use of timber demonstrates more than just visual warmth. Wood is a trusted, fire-safe, and durable material. For example, if NLT or LVL is exposed to flame, the material chars, forming a protective layer.Along with this important aspect, the use of exposed wood also adds biophilic benefits for the fire station’s employees.
A fire station constructed with wood seems counterintuitive, but that wasn’t the case for the station in Prince George, B.C. Wood was the material of choice for the structure—in part to highlight the area’s history with the timber industrysince the early 20th century.
The 2,500 m2Prince George Fire Hall No. 1—which replaces the former smaller, 60-year-old facility—is actually a hybrid of wood, steel, and concrete.Itaccommodates five drive-through truck bays, an emergency operations centre, a dispatch, and administrative offices.
Several main elements within the hall were conceptualized as being wood, which was used both as a structural material—and as a means of expression.
The apparatus bays, for example, were conceptualized as a wood-lined volume that would be visible from the adjacent street and park. With a large amount of equipment and a number of fixtures that are needed in these bays, the wood surfaces throughout the space provide a calm, simple backdrop.
The 2,500 m2Prince George Fire Hall No. 1—which replaces the former smaller, 60-year-old facility—is actually a hybrid of wood, steel, and concrete.Itaccommodates five drive-through truck bays, an emergency operations centre, a dispatch, and administrative offices.
Several main elements within the hall were conceptualized as being wood, which was used both as a structural material—and as a means of expression.
The apparatus bays, for example, were conceptualized as a wood-lined volume that would be visible from the adjacent street and park. With a large amount of equipment and a number of fixtures that are needed in these bays, the wood surfaces throughout the space provide a calm, simple backdrop.
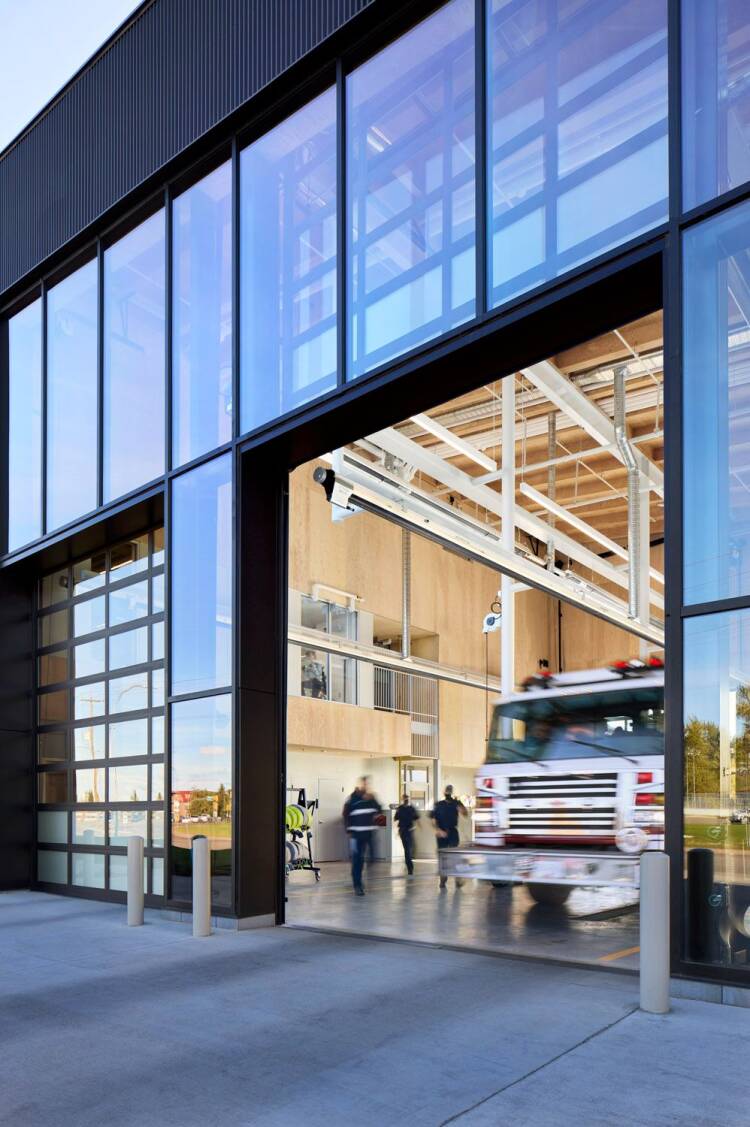

Prince George, B.C.
WINNING PROJECTS
Prince George Fire Hall No. 1
Prince George Fire Hall No. 1
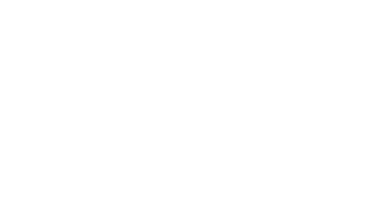

Of course, timber, vs concrete and steel, has no carbon emissions. In fact, timber stores carbon and is renewable if it’s harvested from sustainable forestry production.HAUT is an example of a sustainable structure in other ways. The building is fitted with solar panels on the roof and façade, cooling is sourced from the ground, and sensor-controlled thermostats adjust low-temperature floor heating and cooling. There are nesting boxes for birds and bats, charging points for shared electric cars, and a rooftop garden with rainwater storage.
The design of HAUT has helped to accelerate the shift from traditional construction in concrete and steel to timber as the more sustainable alternative.
The design of HAUT has helped to accelerate the shift from traditional construction in concrete and steel to timber as the more sustainable alternative.
HAUT, the residential apartment in Amsterdam, serves as a prototype for building innovative and environmentally-friendly high-rise timber structures. This 21-floor timber skyscraper received a BREEAM rating of Outstanding, the highest sustainability rating awarded to a residential building in the Netherlands.The total gross floor area is roughly
14,500 m², within which is a commercial/public plinth, cycle storage space, and underground car park. The residential tower, 73 m high, has 52 apartments of different sizes.The load-bearing structure of HAUT is made of CLT panels manufactured off-site, ensuring low waste production and fast, clean on-site assembly. As there are no standard building regulations for high-rise timber construction, the design team has invested much time and energy in technical innovation and safety. Floors and walls are constructed in timber, but a structure made completely of timber in the wet and windy conditions of the city would be impossible. As a result, the foundations, basement, and core are constructed in concrete.
14,500 m², within which is a commercial/public plinth, cycle storage space, and underground car park. The residential tower, 73 m high, has 52 apartments of different sizes.The load-bearing structure of HAUT is made of CLT panels manufactured off-site, ensuring low waste production and fast, clean on-site assembly. As there are no standard building regulations for high-rise timber construction, the design team has invested much time and energy in technical innovation and safety. Floors and walls are constructed in timber, but a structure made completely of timber in the wet and windy conditions of the city would be impossible. As a result, the foundations, basement, and core are constructed in concrete.
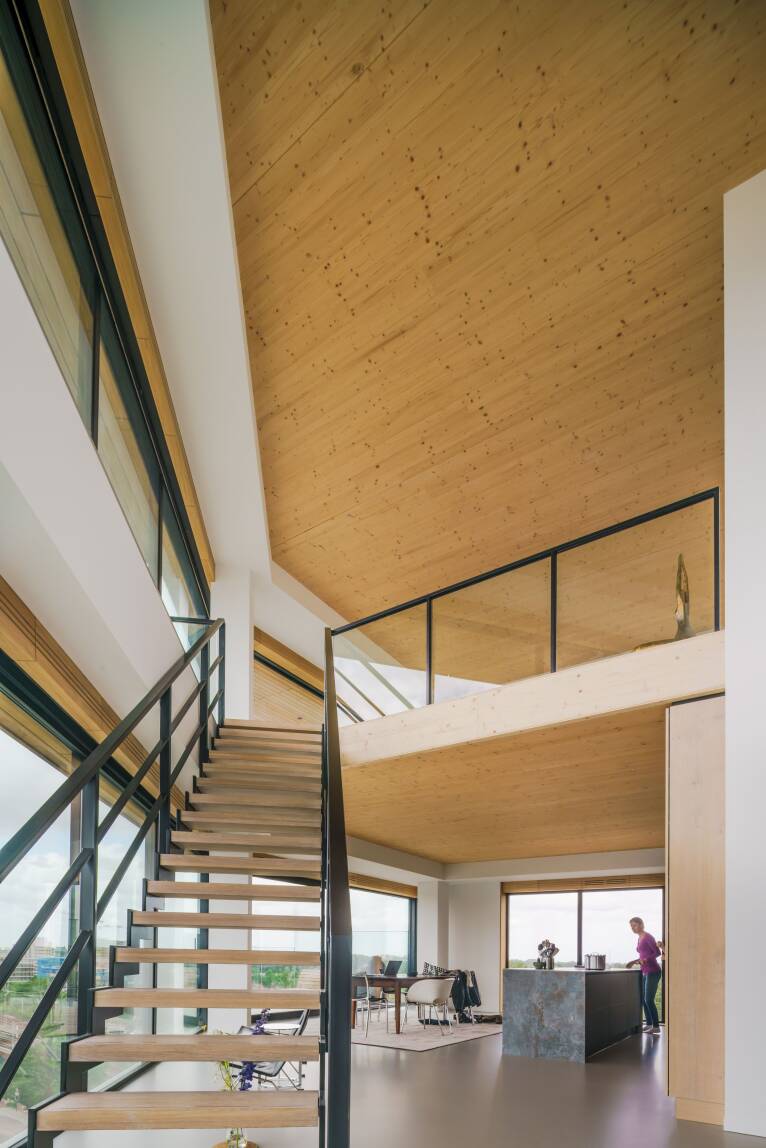

Amsterdam,
The Netherlands
The Netherlands
WINNING PROJECTS
HAUT
HAUT
WOOD CHIPS
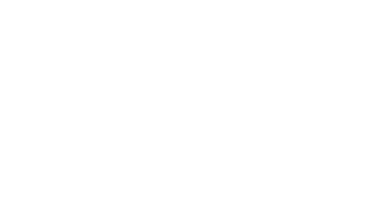

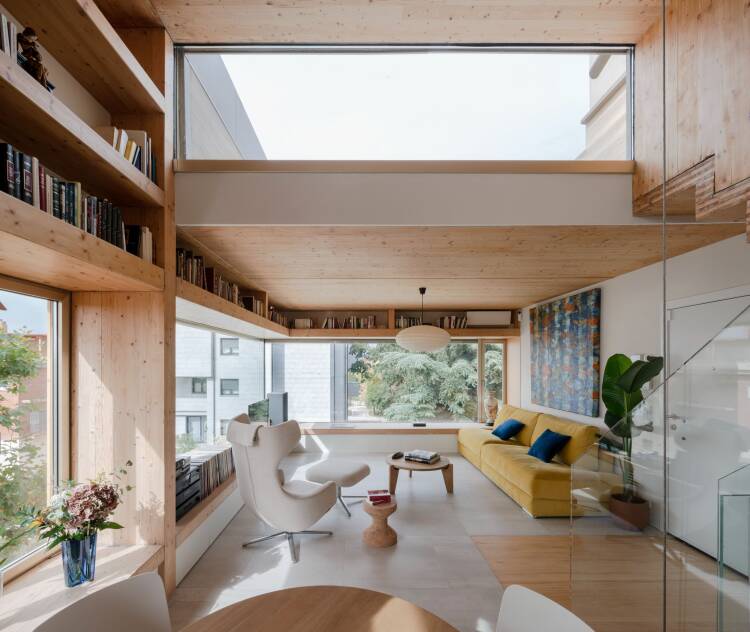

Madrid, Spain
Our-Shelves-Houses in Madrid, Spain, is a co-op building of eight duplex houses that share a common access area and two vertical communication cores. Each of the eight houses has three bedrooms, each room is staggered, and there is elevator service on all floors. The complex also has a swimming pool, garden, and parking.
The co-op building is set back to allow access to Hernández Rubín Street, creating an area for common private use. In the rear area, there is another garden space for common private use.
All of the apartments have a private outdoor space, a garden (for the lower apartments) or a terrace (for the upper ones). In addition, the building offers unique features that allow each co-op member to customize their own home.
The wooden structure allows for sun protection, privacy control, and integrated furniture, among other elements. The staggering of the floors improves communication between rooms and provides for visual connections with terraces and gardens.
The structural system of the five-storey building is composed of CLT panels and laminated wood elements. The CLT panels form the floor slabs and also appear on the façade combined with some glulam beams forming “ribs” for the building envelope. The first floor is formed by a concrete slab, reinforced by its contact with the ground, and steel struts at the corners to solve the overhangs.
The CLT and GLT structure of spruce and pine, and the GL24h class CLT slabs on ceilings, offer sustainability, hygrothermal, and easy assembly advantages.
The use of CLT as a load-bearing material allowed it to be the finishing material, which reduced the project’s labour and execution time.
The building’s installations are resolved by means of an aerothermal system with heat exchange that ensures hygrothermal comfort and ventilation of the apartments with maximum efficiency. In addition, a rainwater collection system is used to use rainwater for irrigation and toilets, and solar thermal panels support the aerothermal machines. Finally, the apartments have mechanical ventilation with heat recovery, ensuring the correct ventilation of each room without the need to open the windows.
The co-op building is set back to allow access to Hernández Rubín Street, creating an area for common private use. In the rear area, there is another garden space for common private use.
All of the apartments have a private outdoor space, a garden (for the lower apartments) or a terrace (for the upper ones). In addition, the building offers unique features that allow each co-op member to customize their own home.
The wooden structure allows for sun protection, privacy control, and integrated furniture, among other elements. The staggering of the floors improves communication between rooms and provides for visual connections with terraces and gardens.
The structural system of the five-storey building is composed of CLT panels and laminated wood elements. The CLT panels form the floor slabs and also appear on the façade combined with some glulam beams forming “ribs” for the building envelope. The first floor is formed by a concrete slab, reinforced by its contact with the ground, and steel struts at the corners to solve the overhangs.
The CLT and GLT structure of spruce and pine, and the GL24h class CLT slabs on ceilings, offer sustainability, hygrothermal, and easy assembly advantages.
The use of CLT as a load-bearing material allowed it to be the finishing material, which reduced the project’s labour and execution time.
The building’s installations are resolved by means of an aerothermal system with heat exchange that ensures hygrothermal comfort and ventilation of the apartments with maximum efficiency. In addition, a rainwater collection system is used to use rainwater for irrigation and toilets, and solar thermal panels support the aerothermal machines. Finally, the apartments have mechanical ventilation with heat recovery, ensuring the correct ventilation of each room without the need to open the windows.
WINNING PROJECTS
Our-Shelves-Houses
Our-Shelves-Houses
WOOD CHIPS
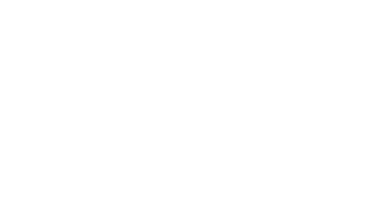